Duplicating Lightning via Vector Fields, Opera
Groundbreaking aircraft lightning-strike simulation project by Cobham Technical Services heralds easy protection design for modern composite structures.
Latest News
April 1, 2010
By Lois Lee
Commercial passenger aircraft are struck by lightning an average of once a year and powerful strikes can result in costly delays for inspection and repair. While the industry’s current certification against lightning—based on threat levels derived from measurements of cloud-to-ground strikes—has served well for traditional airframes with good metallic conduction, modern aircraft built of composite materials are more susceptible to direct damage.
![]() This physical test rig was used to conduct lightning-strike tests of a helicopter at Eurocopter’s Donauwörth facility in Munich, Germany. The tests verified the accuracy of Opera FEA models. |
Industry’s use of increasing amounts of lightweight composite materials in airframes has redirected simulations aimed at discovering the effect lightning has on composites, which are more vulnerable to physical disruption at lightning entry and exit points, and potentially to indirect energy coupling effects in electrical systems as current flows through the aircraft. As a result, it has become increasingly important to understand the exact nature of the threat and develop software to reduce costly testing procedures.
“Airframe structures making extensive use of composite materials have less natural protection against lightning,” says John Hardwick of Cobham Technical Services (Lightning Testing & Consultancy). “As lightning protection measures such as conductive coatings or strips add weight, it’s important to optimize the design, and simulation provides an effective means of achieving this.”
To accrue data on actual in-flight strikes, and help solve the issue of modeling current flow patterns within complete assembled airframes with validated software, the Netherlands’ National Aerospace Laboratory coordinated the In-flight Lightning Strike Damage Assessment System (ILDAS) project. As a first step, the plan was to develop an in-flight embedded system for measuring actual lightning strikes. This would help to better understand the threat, aid the design of lightning protection measures, and streamline post-strike inspections and maintenance by capturing and communicating actual data on occurrences, intensity, and strike points.
The Netherlands’ aerospace lab assembled a team of partners, including Airbus, Air France Industries, EADS Innovation Works, Cobham Technical Services, Eurocopter Deutschland, Groupe Socius, LA Composite, Lufthansa Technik, ONERA, and Technische Universiteit Eindhoven to study and solve the problem.
![]() The Opera user interface from Cobham Technical Services was used to predict the effect of lightning strikes on composite materials used in modern airframes. |
A 3D model used to simulate the effects of the lightning strike was derived from CATIA CAD files of a helicopter assembly provided by Eurocopter. The key issue was to “de-feature” this information, to remove irrelevant data to reduce simulation time, while maintaining accurate models of the electrical impedance of the structure. If the complete CAD data was used, such as the myriad details of fastenings like holes, bolts, rivets, etc., the simulation could literally take years. This detail would add a huge amount of simulation time with negligible benefit to understanding the lightning effects, so it was simplified by filling holes and removing fastenings.
Opera Helps predict current flow
Opera software was used to predict lightning strike current-flow patterns on structures with carbon-fiber composite materials. This knowledge helped ILDAS partners select the best locations for sensors, and then to compare current-flow predictions against actual measurements. To achieve this goal, Cobham Technical Services generated an electromagnetic design model of a specific airframe configuration for an EC135 helicopter using the CAD files from Eurocopter. This part of the exercise mainly involved simplifying non-critical parts of the original design data as stated earlier while maintaining good representations of critical elements. The elements Cobham focused on included metal space frames and surface panels, carbon composite panels, electrical bonding, and cable harnesses such as those for client-specific equipment.
Measurements have shown that the current flowing in a lightning strike has a typical signature. There is a high frequency, low current pre-attachment sequence, followed by the main current pulse, which may last for 200 milliseconds; a sequence of high current bursts with rise and decay times of tens of microseconds occurs during and after the main current pulse. The most severe electromagnetic interference effects occur during the high current bursts, and these were therefore simulated.
The modeling work took around two weeks, but this depended on experience gained from detailed modeling and analysis of typical composite structures, together with comparison with measurements and simulations performed by other partners in the project. Once the model was ready, the simulation itself took a little over a day to run on an office PC. With this supporting work in place, subsequent models of variations on the basic helicopter airframe would be easier and faster to create, providing a simple means of evaluating aircraft construction programs.
Finite element modeling
The Cobham lightning-strike simulation uses a finite element solver and direct time integration. This also provides some significant benefits in terms of both simulation speed and modeling accuracy. Finite element modeling is better at representing the curved surfaces of the helicopter compared with other approaches such as finite difference time domain (FDTD) software (which is used by some aerospace companies). Using the rectangular cells of an FDTD solver can result in models with billions of cells, requiring both high-performance multi-processor computers and very lengthy simulation times (up to weeks) to perform the matrix multiplication required. The finite element solver used in this application—Opera—will simulate a problem of this size on a single-processor PC in about a day.
Physical lightning-strike tests of a helicopter were then completed at Eurocopter’s Donauwörth facility in Munich, Germany, and they verified the accuracy of finite element analysis techniques for characterizing the electromagnetic behavior of complete and custom-cabled modern aircraft structures using advanced composite materials.
These real-life tests at Eurocopter’s facility have shown that the theoretical predictions of energy diffusion effects agreed very well with simulation predictions.
“These real-life tests of ILDAS’s embedded monitoring system concept illustrate how airframe-specific lightning protection can now be accurately evaluated and optimized during the design cycle,” says John Simkin of Cobham Technical Services (Vector Fields Software). “Finite element techniques make it easy to model complex airframe surfaces and important electrical details. The functionality of the Opera geometric modeler made it simple to accept CAD files and reduce the complexity of non-critical elements to ensure rapid simulation.”
More Info:
Cobham Technical Services
Lois Lee manages the U.S. office of Cobham Technical Services (Vector Fields Software). Send comments about this article to [email protected].
Editor’s note: At the time the project started, Culham Lightning and Vector Fields were separate companies. Since then, they have become part of the avionics and surveillance division of Cobham Technical Services. For the purpose of this article, they are referred to as Cobham Technical Services (Lightning Testing & Consultancy) and Cobham Technical Services (Vector Fields Software).
Subscribe to our FREE magazine,
FREE email newsletters or both!Latest News
About the Author

DE’s editors contribute news and new product announcements to Digital Engineering.
Press releases may be sent to them via [email protected].
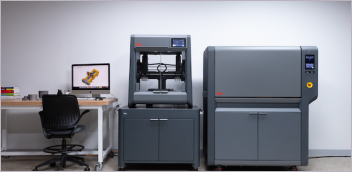
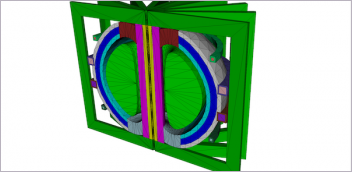
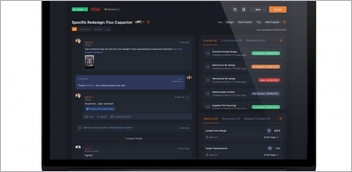
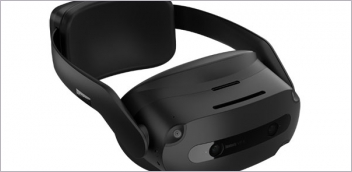