Latest News
August 30, 2009
By Fred C. Jensen
![]() Fatigue strength of selected composite laminates: Cycles to failure at ambient room temperature. |
Composites, used in more and more applications, are now widely used in the transportation industry—including aerospace, automotive, and marine—as well as in a range of applications from wind turbine blades to garden tools. Engineers today should know and understand composites as an integral part of their design toolbox.
Composite construction is defined as a structural material system composed of a combination of two or more materials. In the context of this article we assume the structural material consists of reinforcing fibers such as E-glass (fiberglass), carbon fiber, and some filler material held together by a composite matrix binder or resin.
An important parameter of composite construction is the structure’s fatigue life. The technical literature is now full of composite fatigue data, but composite design requires more care and study by the practicing professional. Caution should be exercised when using commonly published fatigue data for composites because construction techniques and composite material properties can vary widely; high cycle fatigue data should be collected at a slow enough cycle rate so as not to induce hysteresis heating in the composite test sample; and test sample sizes must be representative of the application.
It should be obvious that a composite laminate schedule consisting of crossply construction of plus or minus 45 degree reinforcing ]+/- 45°]s will have a worse cycle life than a laminate schedule with some fibers in-line with the stress direction. For example, the chart above compares the crossply laminate with the quasi-isotropic symmetrically repeating laminate ]0/90/+-45]s. Here the 00 fibers are in-line with the stress direction.
What may not be as obvious is that there is an optimum fiber density for maximum cycle life. Components made with very high percentages of fiber reinforcements do not make for higher cycle lives. A fiber density of 36 to 42 percent in a laminate is about optimum for cycle life. In fact, tensile fatigue resistance drops rapidly as fiber volume is increased above the 40-45 percent range.1 This increase in fatigue sensitivity at higher fiber content is not offset by the higher initial strength. It appears that the fibers need the matrix to keep each single fiber from contacting its neighbor, thus preventing rubbing and bending over each other.
Since composite materials can be good thermal insulators, it is important to be careful not to overheat the test sample with internal friction when collecting high cycle structural data. The test frequency, as recommended by the Automotive Composites Consortium, varies with stress in accordance with the following relation:
Test frequency = k (S ultimate) / (S max – S min)where k was 3 Hz, S ultimate is the UTS of the composite, S max is the maximum stress in the cycle, and S min is the minimum cyclic stress. S min is usually taken as one tenth of S max. See Reference 4 for additional details.
The test sample must be large enough to include the important structural details of the laminate. Testing small bundles of fibers may not give representative results. Reference 5 describes the work of Sutherland, Mandell and Creed, where testing at frequencies up to 100 Hz, shortened the test period for 108 cycles to just 11.6 days. Adequate heat transfer was achieved by using very thin specimens, approximately 0.06 in. thick. One needs to verify that their laminate can be represented by such a thin test sample before using that data.
Some additional comments about designing composite structures for long fatigue life: Reference 1, observed no measurable effect of matrix material on cycle life when comparing good quality unsaturated orthophthalic polyester resins, vinyl ester resins, or epoxy resins.
![]() |
Table 1 describes a few representative laminates widely used in industrial applications. Included is the industry application. Since this is intended to be a short introductory article on composite fatigue life, the reader should refer to the source references listed in the table for critical design work.
The composites listed in Table 1 have their estimated fatigue lives plotted in the line graph above. Even though the chopped stand mat (CSM) composite has the lowest fatigue life of those presented, it is cheap to produce. This allows thick sections to be fabricated, which will lower the over-all stress values allowing good service life in many applications.
Readers should refer to the source references listed in the table for critical design work.
References:
1) “Fatigue Resistant Fiberglass Laminates for Wind Turbine Blades”, Published for Wind Energy 1996, ASME, pp. 46-51, by Daniel D. Samborsky and John F. Mandell, Department of Chemical Engineering, Montana State University, Bozeman, MT 59717.
2) “Principles of Yacht Design”, Second Edition, by Lars Larsson and Rolf Eliasson, International Marine, Camden Maine, 2000, Figure 13.8, Fatigue properties of CSM laminate, page 256.
3) “Basic Properties of Reference Crossply Carbon-Fiber Composite”, ORNL/TM-2000/29, by J. M. Corum, R. L. Battiste, K. C. Liu, and M. B. Ruggles, Oak Ridge National Laboratory, Oak Ridge, Tennessee 37831-6285, February 2000.
4) “Recommended Minimum Test Requirements and Test Methods for Assessing Durability of Random-Glass-Fiber Composites”, ORNL-6953, by J. M. Corum, R. L. Battiste, W. Ren, and M. B. Ruggles, Lockheed Martin Energy Research Corp., Oak Ridge National Laboratory, Oak Ridge, Tennessee 37831-6285, June 1999.
5) “Application of the U.S. High Cycle Fatigue Data Base to Wind Turbine Blade Lifetime Predictions”, Proceeding of Energy Week 1996, ASME, by Herbert J. Sutherland, Wind Energy Technology, Sandia National Laboratories, and John F. Mandell, Department of Chemical Engineering, Montana State University, Bozeman, MT 59717.
More Info:
Patriot Engineering Co.
Fred C. Jensen, MSME, P.E. is director of engineering at Patriot Engineering Co, providing mechanical engineering solutions (design, FEA, CFD, machine / product development and build) since 1979. You can send comments about this article to [email protected].
Subscribe to our FREE magazine,
FREE email newsletters or both!Latest News
About the Author

DE’s editors contribute news and new product announcements to Digital Engineering.
Press releases may be sent to them via [email protected].
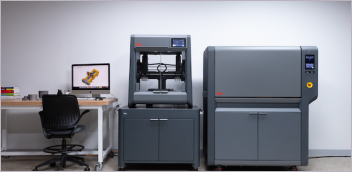
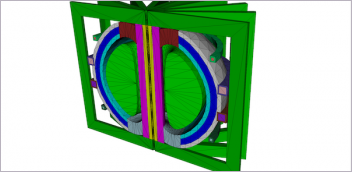
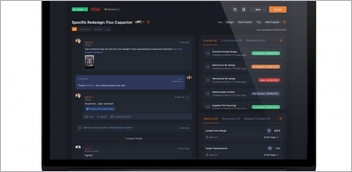
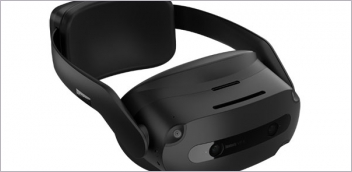