Latest News
January 11, 2012
By DE Editors
In 2007, engineers at the Landoll Corp. in Marysville, KS, began researching options for replacing their existing cost-estimating software. They needed a flexible system that would produce accurate job quotes, and process plans for a wide variety of machining, fabricating and assembly jobs. They also wanted software that was easy to learn and that would provide the company’s cost estimators with the ability to quickly calculate process cycle times and costs.
Landoll’s Manufacturing Engineering Supervisor, Alan Koch, who participated in the search for a new system, says his department realized those benefits and more when they began using the Costimator cost estimating, quoting and process planning software by MTI Systems Inc. The system’s database of materials, work centers and process cost models allowed for quick, easy implementation and a short learning curve, according to the company.
Example 1: Tillage walking beam (left) with a detail of the walking beam tube.
The software’s benefits multiplied a year after the estimating system installation, Koch adds, when Landoll upgraded to the latest version of the Costimator software. This was when MTI Systems, located in West Springfield, MA, developed the system’s new Cost Modeler feature. MTI says this cost model-building tool enables estimators to generate cost estimates up to 70% faster than traditional estimating methods.
“Cost Modeler requires far fewer inputs by the estimator, and yet it generates cost estimates that are more accurate and consistent,” says Koch. “We have found the software easy to use, even when the end user has minimal computer experience or limited manufacturing knowledge. Our cost estimators—who work in a time-sensitive and highly competitive manufacturing environment—now can produce consistently accurate estimates, regardless of their manufacturing experience.”
Winning Jobs in a Competitive Market
Founded in 1963, the vertically integrated Landoll Corp. designs, fabricates, finishes and markets a varied product line of light and heavy equipment. The products are mostly for the farming industry, and include heavy equipment trailers, specialized narrow-aisle forklifts, agricultural tillage equipment and earthmoving equipment. Additionally, Landoll Corp. has built military tactical vehicles for the U.S. Air Force, Army and Navy over the last 25 years.
Landoll is tasked with designing and quoting single parts, assemblies and entire pieces of heavy equipment. It also bids on government manufacturing contracts and jobs for original equipment manufacturers (OEMs) such as Caterpillar, Snorkel, FMC, John Deere, Altec and Monosem, to name a few.
Scott Padgett, who began working at Landoll in 1993 as a design engineer, transferred to the industrial engineering and cost-estimating departments. He was tasked with implementing the new Cost Modeler feature, as the “master engineer” for Costimator responsible for finalizing the cost models for end users in his department. He found that the Cost Modeler tool significantly streamlined the company’s cost-estimating and job-quoting processes.
“Landoll has both manual and CNC machines, and we have diversified our lines to protect us from the up-and-down economy,” Padgett says. “We need to estimate and quote all types of jobs, whether piece parts, weldments, assemblies or finished products for trailers, tillage or forklifts. The Cost Modeler feature enables us to do all that quickly.”
![]() Example 2: A screen capture of a CNC Tube Laser operation. |
A Closer Look
Given the flow of requests-for-quotes into his department, Padgett “tweaks” existing cost models and builds, as needed, inputting data from manufacturing time studies he occasionally conducts on the shop floor, as part of his regular information extraction tasks. The cost models that came with the system are easy to modify, and creating new ones is very straight forward, he says.
Most of Padgett’s time on Cost Modeler, however, is spent working on competitive quotes. To provide an end user’s view of Cost Modeler, the engineer reviewed an estimate for a three-component tillage walking beam (see Example 1).
He specified a screen capture of a CNC Tube Laser operation to manufacture the walking beam tube component of the part (see Example 2), explaining that he simply responded to screen prompts for each of the job’s operations, referencing the part drawing and inputting information such as number of parts, shape of material, part length and thickness, and type of cut.
Once that information is entered for an operation, he explains, the software will estimate its manufacturing time. To complete the calculations, the software draws data from both Cost Modeler and the Costimator system’s vast database of machining times and labor standards.
“Cost Modeler not only saves time, it takes all the guesswork out of our estimating—so once the user inputs basic information on the size of a part and its features, the software does the work for us,” says Padgett.
Padgett concludes that everyone at the company, from salespeople to managers, is now much more efficient because of the cost models available in Costimator.
Subscribe to our FREE magazine,
FREE email newsletters or both!Latest News
About the Author

DE’s editors contribute news and new product announcements to Digital Engineering.
Press releases may be sent to them via [email protected].
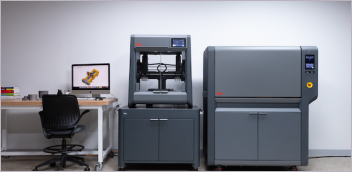
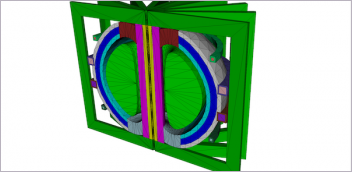
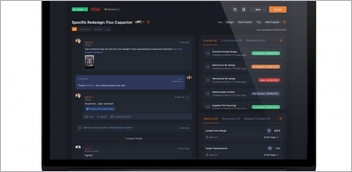
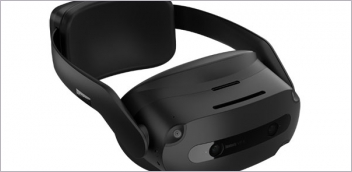