Fast App: Streamlining Intelligent Control Valve Design
Simulink, xPC Target, and MATLAB used to speed up HUSCO's electrohydraulic valve design process for excavators.
Latest News
August 1, 2010
By Corey Quinnell
High fuel prices and growing sensitivity to environmental issues are forcing off-highway OEMs to re-evaluate their product architecture and technology. To stay competitive, manufacturers of excavators, earth-moving machines and other heavy-duty industrial equipment are constantly seeking new ways to improve efficiency and reliability, while continuing to meet safety standards and reduce costs.
![]() HUSCO International was able to capitalize on its INCOVA technology for excavators by getting the design to market quickly. |
Electronic control of hydraulic systems has been touted as one way to improve vehicle efficiency and controllability, but there are design tradeoffs to consider.
HUSCO International, which develops and manufactures hydraulic and electrohydraulic valves and controls, recognized this need and developed the Intelligent Control Valve (INCOVA) technology. Instead of controlling flow with traditional spool-and-sleeve valves, INCOVA incorporates independently controlled electrohydraulic poppet valves with an electronic controller and built-in transducers to measure cylinder workport pressures. The INCOVA technology provides electronic load sensing and pressure compensation, quickly opening and closing valves as the load varies to maintain a constant velocity. This increases overall fuel efficiency and productivity, and improves uptime and diagnostics.
HUSCO realized it was only a matter of time before other manufacturers would introduce similar products to stay competitive. To answer that, the company needed a faster, more efficient design process—with shorter design iterations and development time to speed time to market.
![]() The MathWorks’ Simulink was used to segment the model and divide the design effort among specialized engineers. |
In HUSCO’s former design process, systems engineers captured control requirements in a Microsoft Visio diagram. Software engineers then used this diagram as a specification to manually write C code for the control system. With no way of numerically validating the requirements captured in static diagrams, HUSCO’s software engineers had to interpret and hand-code both the original design and all subsequent changes. That meant long delays between the capture of a control algorithm and the ability to validate it on a machine. This process made it difficult to complete multiple design iterations. But by using The MathWorks tools and model-based design, the engineering team was able to implement a streamlined design process to help speed product design without compromising quality.
An Integrated Approach
Engineers designed, modeled and validated the INCOVA control system using Simulink software. They then used Real-Time Workshop to generate C code from their Simulink models and xPC Target to implement a real-time prototype. A graphical user interface developed with MATLAB GUIDE tools was used to input the machine’s system parameters, which included items such as the number of hydraulic cylinders and velocity requirements of each cylinder.
INCOVA System engineers also used Simulink to develop the control algorithms that translate joystick movement to cylinder movement. Simulink enabled them to segment the model and divide the design effort among engineers specializing in filter design and proportional integral-derivative (PID) controllers.
After assembling all subsystems into a complete Simulink system model, comprised of more than 1,000 blocks, the team was able to design, debug and tune the control system from their desks. In this way, Simulink provided a safe testing environment, which would not be possible when working on a live excavator.
To visualize simulation results, the team used MATLAB to post-process the captured output, calculate energy consumption and plot joystick position vs. cylinder movement. HUSCO software engineers generated C code from the Simulink model using Real-Time Workshop. They then used xPC Target and xPC Target Embedded Option for standalone operation of the control code on real-time PC hardware from Speedgoat, an xPC Target system integrator.
To validate the control system, the team developed a plant model of the excavator in Simulink. They linked the plant model with the control system model running on xPC Target. The validated control system was then connected to the actual excavator for further live testing and fine-tuning.
The excavator is currently operating with the control system running on xPC Target. HUSCO plans to use Real-Time Workshop Embedded Coder to generate code for its target production hardware.
In the past, systems engineers had to consider hardware details such as the number of bits of accuracy and worry about communicating the design to the software engineer. HUSCO’s new design method enabled its systems engineers to focus on controls, not on the details of the target hardware. Ultimately, this streamlined process cut development time by more than 50%—from six or seven months to two or three. Design modification time decreased significantly because no handwritten code changes were required with every design change.
Perhaps the best result for HUSCO was that 100% of the controls system design is now reusable. The team customized its Simulink model to account for varying numbers of cylinders, making it reusable in development of future control platforms for different machines.
More Info:
INCOVA Technologies
MathWorks
HUSCO International
Corey Quinnell is a systems engineer for INCOVA Group at INCOVA Technologies, Inc. Comments should be sent to [email protected].
Subscribe to our FREE magazine,
FREE email newsletters or both!Latest News
About the Author

DE’s editors contribute news and new product announcements to Digital Engineering.
Press releases may be sent to them via [email protected].
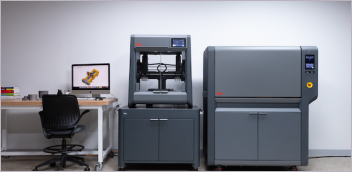
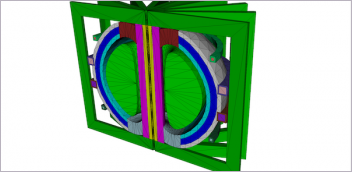
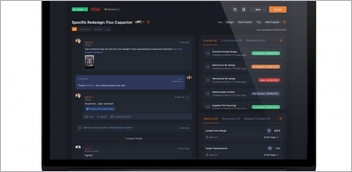
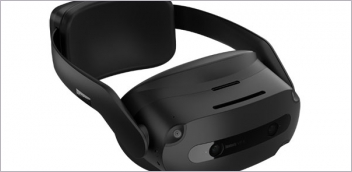