Fraunhofer and Concept Laser Partner for Large-Scale Additive Manufacturing

Concept Laser’s X line 1000R offers large-scale AM for the automotive industry. Courtesy of the Fraunhofer Institute.
Latest News
December 13, 2012
Big business is looking into new ways of adapting additive manufacturing (AM) to improve not only the design process, but the production process as well. In the aerospace industry, Airbus and Aerosud are developing large scale AM facilities to produce major components of aircraft (such as entire wings). Now the automotive industry has invested in large-scale AM.
The Fraunhofer Institute of Laser Technology has partnered with Concept Laser to produce a large-scale AM system at the behest of Daimler. This is a story I’ve been following for a while, but details have been sparse. Euromold 2012 provided a few missing puzzle pieces, which I can now share with confidence.
The X line 1000R is being touted as one of the largest AM systems ever built. It has a build envelope of 630 × 400 × 500 mm (23.6 x 15.7 x 19.7 in.), and the build bed rotates to help reduce build times. The new system has a layer thickness of 20-100 μ.
“This really was uncharted territory for us,” said Frank Herzog of Concept Laser. “The development of a machine concept of these dimensions in close collaboration with Daimler AG and the Fraunhofer ILT clearly illustrates our claim to be the technology leader in the field of laser melting.”
The X line 1000R uses Concept Laser’s LaserCUSING process, which, according to the company, produces metal AM-created objects with greater durability and density than other laser sintering processes. Potential materials include high-grade steel alloys, tool steels, aluminum or titanium alloys, nickel-based super alloys, and cobalt-chromium alloys.
Daimler approached Concept Laser and the Fraunhofer Institute to design an AM system that could replace sand and die-casting processes. The lack of waste associated with AM means long-term savings for Daimler, as opposed to more traditional methods of manufacturing.
Size wasn’t the only goal. Daimler also insisted on a system that was significantly faster than Concept Laser’s other machines. According to Concept Laser, this was achieved by fine tuning temperature control inside the reaction chamber and the powder bed. The first X line 1000R has already been delivered to Daimler.
Some details of the system are still under wraps, which means no video of the X line 1000R, but below you’ll find a video that demonstrates the LaserCUSING process on a smaller Concept Laser system.
Sources: Fraunhofer Institute of Laser Technology, Optics.org
Subscribe to our FREE magazine,
FREE email newsletters or both!Latest News
About the Author
John NewmanJohn Newman is a Digital Engineering contributor who focuses on 3D printing. Contact him via [email protected] and read his posts on Rapid Ready Technology.
Follow DE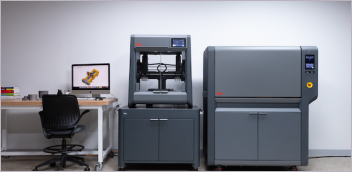
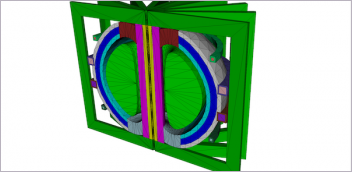
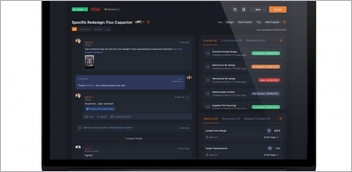
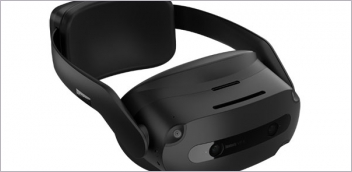