Latest News
December 20, 2007
By Sara Ferris
![]() The Nucleus Freedom from Cochlear converts sounds to digital signals, then uses the signals to stimulate the hearing nerve in the inner ear. |
Longtime Pro/ENGINEER user Cochlear Ltd. (Sydney, Australia) has added PTC’s Windchill content and process management product to its operations. Cochlear designs and manufactures implantable hearing solutions, operating in more than 90 countries to support the more than 130,000 recipients of its cochlear and bone conduction implant technology.
To support its growth strategy, Cochlear aims to bring regular new products to market, and the capabilities of Windchill offer numerous operational efficiencies in support of this goal. In particular, the company relied on paper-based systems for managing product information and recognized that that a new system that digitally manages its product data would facilitate numerous process improvements. Cochlear also hopes to improve the visualization of the maturity status of parts and assemblies as they move forward in their development.
Cochlear deployed Windchill to improve product development processes such as product change control, release to ERP (enterprise resource planning), part promotion lifecycle maturity, and Bill of Materials/Bill of Tools configuration management.
Windchill makes the design process more efficient by controlling and automating the product change control processes. Additionally, by enabling reuse of previously designed product configurations, Windchill helps promote the rapid development of new product configurations.
![]() The Baha system from Cochlear uses the skull bone to transfer sounds to a functioning cochlea. |
Cochlear anticipates that it will achieve significant improvements in the speed of internal review and approval of product changes. It also expects improved efficiency in creating, archiving, and storage of electronic product documentation; a faster, more efficient product design review process; better worldwide visualization of all product data (e.g., designs, BOMs, status of product maturity); and quicker release of product information from design to manufacturing.
“To support our business growth, we recognized the requirement to move from a paper-based system to an electronic management system,” said Brent Barnes, manager of documentation systems, Cochlear. “The PTC Product Development System improves visibility of product changes and product maturity, and continues to enforce quality and regulatory controls to maintain strict compliance at all times.”
“PTC’s integral product development system offers significant benefits to medical device companies by enabling them to essentially ‘hard wire’ compliance into the product development process,” says David Rubin, director, market strategy, medical devices and life sciences, PTC.
Sources: Press materials received from the company and additional information gleaned from the company’s website.
Subscribe to our FREE magazine,
FREE email newsletters or both!Latest News
About the Author

DE’s editors contribute news and new product announcements to Digital Engineering.
Press releases may be sent to them via [email protected].
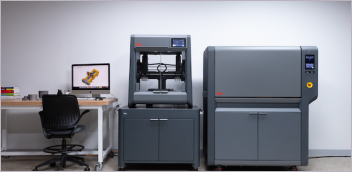
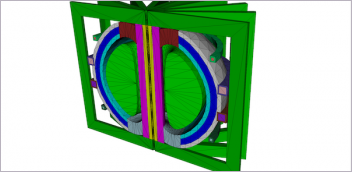
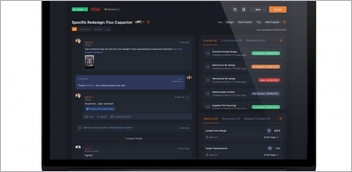
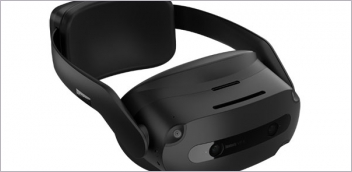