Latest News
May 16, 2018
GE Additive reports that the Arcam EBM Spectra H, its recently unveiled electron beam melting (EBM) metal additive manufacturing system, is designed to handle high heat and crack-prone materials such as titanium aluminide (TiAl). The company also says that the Arcam EBM Spectra H incorporates a range of new features and enhancements intended to drive down the costs of high-volume industrial production by increasing system productivity.
One of the Arcam EBM Spectra H’s new features and enhancements cited by GE Additive is an increased build speed of up to 50% compared with current EBM machines. This, the company explains, is in part due to a 6kW HV-unit beam that reduces all pre- and post-heating steps. Additionally, heat management has been improved through the incorporation of a movable heat shield that keeps heat in the build area.

The Arcam EBM Spectra H delivers a 9.84x16.9-in. (250x430 mm) build volume, which is approximately 39% larger than current EBM machines. The company adds that an improved layering procedure reduces the need for heating, saving approximately five hours for a full height build.
The Arcam EBM Spectra H, as well as the company’s Qplus EBM systems, will incorporate Arcam xQam automatic calibration technology. This technology, the company says, improves position and focus accuracy, while eliminating the need for manual calibration. The net effect, it explains, is that the process time is reduced from three to four hours to 15 minutes.
The Arcam EBM Spectra H provides a dust-tight environment in all steps of the process that maintains powder batch integrity, reduces the risk of contamination and protects the operator from the powder. Features of the system include automated, self-dosing sieve and hopper filling station processes, automatic powder hoppers and automated powder recovery. The all-new powder distribution system produces repeatable and reliable parts, according to the company website.
The Arcam EBM Spectra H, which complements the company’s existing line of EBM systems, is available for pre-order. It will be manufactured at Arcam’s facility near Gothenburg, Sweden. Shipments are expected to begin in the fourth quarter of 2018, according to the company.
Initially, the Arcam EBM Spectra H will support both TiAl and nickel Alloy 718 materials. The company adds that it plans to offer additional nickel-based superalloys in 2019. GE Additive also reports that its materials science team is currently exploring future opportunities for a wider range of high-heat materials, including nickel superalloys, tungsten, cobalt-chromium, stainless steel and metal matrix composites.
“This new system shows our commitment to developing industry-leading additive machines, materials and services,” said Jason Oliver President and CEO, GE Additive, in a press statement. “We remain focused on accelerating innovation across sectors and helping the world work smarter, faster and more efficiently.”
For more details on the Arcam EBM Spectra H additive manufacturing system, click here.
Watch the Arcam EBM Spectra H introductory video.
See how the Arcam EBM Spectra H’s additive manufacturing process works.
Read more about Arcam’s materials.
See why DE‘s editors selected the Arcam EBM Spectra H as their Pick of the Week.
Sources: Press materials received from the company and additional information gleaned from the company’s website.
Subscribe to our FREE magazine,
FREE email newsletters or both!Latest News
About the Author

Anthony J. Lockwood is Digital Engineering’s founding editor. He is now retired. Contact him via [email protected].
Follow DE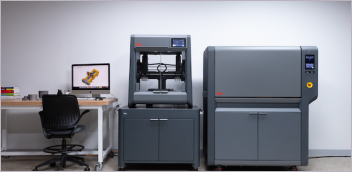
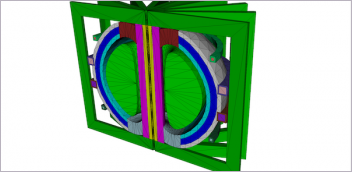
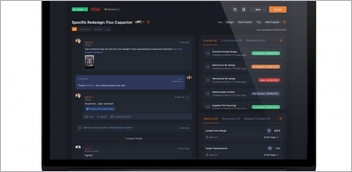
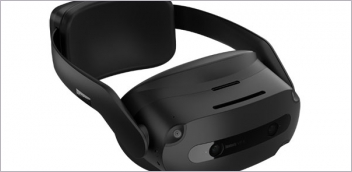