Latest News
March 3, 2016
Boris Marovic is the industry manager for Automotive and Transportation in the Mentor Graphics Mechanical Analysis Division, Frankfurt, Germany. He studied aerospace engineering at the University of Stuttgart majoring in aircraft design and aerodynamics and started with Mentor Graphics (formerly Flomerics) as an application engineer.
Pam Waterman, contributing editor to Desktop Engineering, caught up with Marovic to ask about democratizing simulation software by making it more accessible to small- and medium-sized businesses.
Q: What do you say to potential small- and medium-sized customers to illustrate you understand the many angles of their businesses?
A: Often small- to medium-sized businesses can’t afford computational fluid dynamics (CFD) specialists or high-performance computing clusters for a fast turnaround time of simulations. And, even if they can, traditional CFD tools are complicated and cumbersome, not conducive to a fast and agile product design process. Even larger companies don’t want their design engineers spending several days on creating a computational mesh. If they outsource it to India or China, they still have to wait for the mesh to run their simulations; and as soon as the design changes, the process starts over … of course, the design can change daily, even every hour, for smaller adjustments.
Whether done in-house or outsourced, the traditional CFD approach is slow and inefficient for today’s manufacturing design process. For example, imagine that the driver-assistant systems of your car that should prevent you from accidentally switching lanes gives you feedback after you are already halfway into the other lane. That’s not a useful system. Similar is true for time-consuming CFD processes used to evaluate design changes, to see if the changes are going in the right direction and whether you need to decrease the temperature or pressure loss to increase the efficiency of the product.
Engineers want to know the answer to their design changes quickly because they have a deadline, and often the product needs to get onto the market to beat the competition by a few days or even weeks. Let’s say you have a deadline for the final design in two weeks (10 work days), and your CFD simulations take four to five days to get back to you. Although you can change the design within one to two hours to adjust it once you have the results of the simulation, you are only able to only run two more iterations, and then the third design has to go into production.
In comparison, the CAD-embedded CFD approach provided by FloEFD enables automatic meshing in minutes to hours rather than days; as a result, engineers are able to set up the boundary conditions, run the simulation, and get some results within one to two days. This allows them to run five to 10 design iterations and gives them more time to improve the product than any of their competitors who are following the traditional CFD process.
Q: What does Mentor Graphics offer to lower or eliminate their barriers to entry?
Often, when people think about CFD, they throw up their hands in horror because they see it as a science rather than an engineering discipline. Our software developers and scientists didn’t spend their time creating a scientific tool that requires only scientists to use it; instead, they created an engineering tool that has the know-how of CFD science built into its core. You don’t have to have a Ph.D. degree to be able to use FloEFD because the Ph.D.-level of knowledge is basically built into the product. Our focus lies on providing a sophisticated tool that is easy to use. For example, as with every smartphone or tablet, most people don’t know how they work, but no one has a problem using them. So we thought: “why not do the same for CFD?”
FloEFD is easy and efficient to use because it is a CFD tool that is built right into CAD environments, such as Siemens NX, PTC Creo and CATIA V5, so that design engineers can run simulations directly on their particular CAD model without leaving their preferred environment. Design engineers know the boundary conditions under which their product is running because they designed it for those conditions. All that they have to do in FloEFD is define those conditions from the model: the material, any heat sources, or what fluids it operates in or with. Once that is done, the FloEFD mesher runs automatically; the designer simply clicks “Run mesher,” and the rest is done by the computer.
Creating a mesh is a major barrier when working with CFD. The worst part comes once you think the mesh is good, and then the solver for some reason diverges and doesn’t come to a solution. FloEFD’s solver is so stable that the designer would have to apply irrational boundary conditions for the solver to diverge and not come to a solution. The stability is a result of the mesher and solver being built for each other. FloEFD’s solver only works with its meshing technology and vice versa. In most CFD tools, you can create a range of different meshes and cell types, and then you have to consider the numerical influences of them and their interactions, etc. FloEFD produces the mesh that fits the solver that produces the results, providing much faster and reliable results.
Q: How can you get SMBs started and make them comfortable with their investment of money and effort?
First, anyone who’s interested can try out the product online in our Virtual Lab. Here, they can get a feeling for how FloEFD works without having to install the product. We also provide tutorial models to help anyone getting started. If you try it out and like the program, you can contact us and ask for a benchmark on your models against measurements or do it yourself with an evaluation. We will provide you with a training to make sure you do everything right and can handle the software yourself and really feel and see the benefit of a CAD-embedded CFD tool.
We find that many people are up and running with the software in about eight hours. However, if you need more guidance, our team provides you with consulting work and can help you through a job/project. Our engineers are here to help you with any questions you may have while you repeat the workflow the first few times until you get used to it. We also provide a worldwide support service online where you can reach someone any time of the day to help you with your task.
Q: Is cloud-based software “the only way to go” or is there still a good role for traditionally sourced programs?
FloEFD is not cloud-based; however, you can test FloEFD for 30 days on the cloud with a browser so that you don’t have to install it on restricted IT systems. Certainly, cloud-based solutions can be used to outsource computing resources, but then the information is out there somewhere on the cloud and not in your company’s controlled network. Often, simulations can create large results especially if calculations were done for transient simulations and several result files are created. This kind of data transfer is massive, such as 100GB, and not everyone can afford the time or money required. FloEFD makes CFD available for anyone who wants to use it; they don’t have to have huge resources behind them to get good results.
Cloud networks are great for sharing your videos or images with family and friends via Dropbox, iCloud, Google Drive, or other services. However, for our customers who are concerned about the security of their IP (intellectual property) and confidentiality, whether they are automotive, aerospace, military or consumer goods manufacturers, keeping development data on the public cloud isn’t currently a viable solution.
Q: Should a small business, getting started, always use a general-purpose analysis software, or the opposite, an application-specific package/module?
A small business has basically three different options when deciding on a simulation tool. Some programs are very specific for an application and allow a sort of “appification” of their tool where the user interface can be dumbed down to only the necessary features compared to the full tools capability. Secondly, tools such as FloEFD build in easy simulation while keeping the high-end capabilities. Thirdly, specialized tools are useful if you only have one type of application to simulate, such as for injection molding applications. But what if you want to consider not just the injection but also the mold cooling? Can the tool simulate that as well?
High-end tools that were appified for non-CFD experts end up requiring a lot of support and maintenance because as the engineering task grows, new features have to be implemented in the app and the development effort to constantly add features that are present in the full tool but were not in the app-version can be quite expensive. In that way, it is almost like maintaining software for which you have already paid maintenance but now you may need to add an employee to update and support the updated appified version, an expensive proposition.
Our philosophy is that any user interface can be adapted to the engineer’s usual working environment, and in most cases, this is the CAD system where the product takes shape. Any requirements for a simulation that can be communicated by an engineer can also be “communicated” via the programming to the computer, that is, built into the software. Our goal is to provide increasingly better usability of our products so that the really challenging tasks that take a lot of time and expertise on a daily basis can be put into the software, somewhat automated, so that the person who doesn’t have to do simulations every day is still able to use the tool in his or her CAD environment as needed and get good results quickly.
FloEFD can be customized for specific applications, such as hypersonic flow, combustion, or work with electronics cooling applications, by purchasing modules. By keeping these specialties as add-ons, it keeps the price down for everyone else who doesn’t need those applications. We make sure the modules only add the physics and features needed, not adding to the complexity of the tool use, so that customers can increase the possible applications and simulation accuracy as they see fit.
Q: How are user-written apps being encouraged and supported?
As mentioned, FloEFD doesn’t provide full control from the outside via an API (application programming interface) to create user-written apps. But we do provide an API so that engineers can control a simulation setup from a tool outside of FloEFD, such as Excel via Visual Basic, Visual Basic for Applications and Visual C++. Sometimes engineering students do this as part of their thesis or others use it to automate more of their work. Most CAD systems also have an API, which can be used to change geometries.
Engineers who are working on the CAD models don’t have to be software programmers to fully manipulate the simulation settings and meshing, etc., in FloEFD, unlike other tools where CFD experts need to be involved who have experience in programming.
More Info:
Subscribe to our FREE magazine,
FREE email newsletters or both!Latest News
About the Author

Pamela Waterman worked as Digital Engineering’s contributing editor for two decades. Contact her via .(JavaScript must be enabled to view this email address).
Follow DE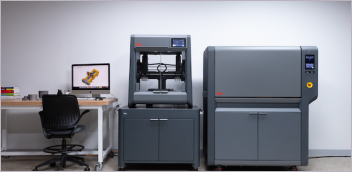
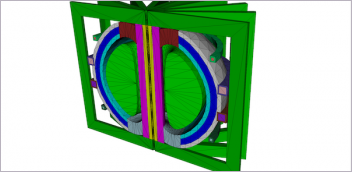
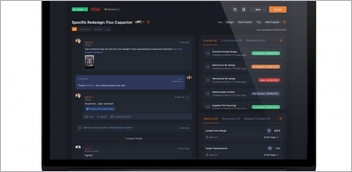
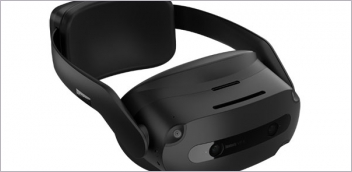