Quickparts Assists NASA Space Shuttle Endeavour
Re-entering the Earth's atmosphere just got safer.
Latest News
August 1, 2008
By Quickparts
![]() |
Recently Quickparts was contacted to build a custom-designed part that would act as a housing for the new wireless scanner developed to scan the surface tiles of the space shuttle Endeavour. The Scanner is designed to locate and evaluate cracks and imperfections on the tiles that line the surface of the shuttle.
Challenge
The housing needed to be built very quickly, and had to be in a production quality material that could withstand regular use over extended periods of time without breaking.
Solution
Fused Deposition Modeling (FDM) is a solid-based rapid prototyping method that extrudes material, layer-by-layer, to build a model and was an ideal candidate for the job. The build material, production quality thermoplastics, is melted and then extruded through a specially designed head onto a platform to create a two-dimensional cross section of the model. The cross section quickly solidifies, and the platform descends where the next layer is extruded upon the previous layer. This continues until the model is complete.
Using Quickparts instant quote technology, QuickQuote®, NASA was able to receive instant pricing and continue to move the project forward. Quickparts was able to build and start shipping parts to NASA in a week. This is a prime example of rapid manufacturing being used in a final product. There is no need for expensive tooling; therefore these custom-designed parts can be made quickly, inexpensively, and at any time.
Results
The new scanner will replace the old manual way of inspecting tiles. Previously technicians had to visually inspect and measure cracks and dings with small scales. Six NASA technicians are using the scanner to inspect every one of the 24,000 tiles that cover the space shuttle Endeavour in preparation for the new launch. Each scanner weighs less than 3 pounds and is the size of a small teapot. The scanners capture the length, width, and depth. This data is then sent to a computer in roughly 3 seconds for scrutiny by NASA technicians.
“The new method is much faster and more accurate because the depth and volume measurements of the flaws and their locations are wirelessly transmitted into a computer database,” said Joe Lavelle, a senior engineer and project manager at Ames. “This tool allows the inspectors to determine with very high confidence whether a shuttle tile needs to be replaced or just repaired….When they made the measurements manually with the scales, they had to estimate the volume of flaws to a worst-case value because they could not precisely measure the volume with any accuracy,” Lavelle explained. “With this scanner, they will actually save tiles and the time-consuming process of replacing them.” The tiles that line space shuttles protect the shuttle and its occupants from the extreme heat generated from re-entry into the Earth’s atmosphere.
More Info:
Quickparts
301 Perimeter Center North, Suite 500
Atlanta,GA 30346
P: 770.901.3200; F: 770.901.3236
quickparts.com
Subscribe to our FREE magazine,
FREE email newsletters or both!Latest News
About the Author

DE’s editors contribute news and new product announcements to Digital Engineering.
Press releases may be sent to them via [email protected].
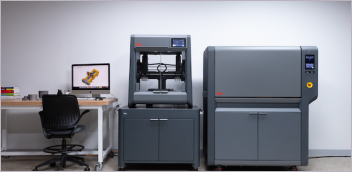
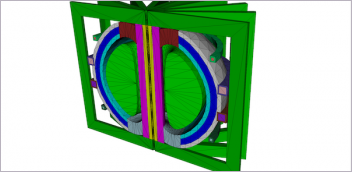
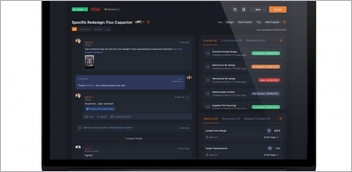
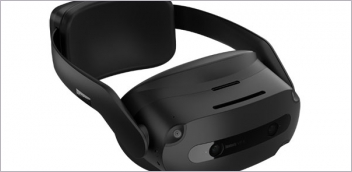