Renishaw, Materialise Take Steps to Advance Production-grade Metal AM
Partnership enables seamless workflow integrations and customizable print processors that help shorten production time.

Materialise’s next-generation build processor complements Renishaw’s TEMPUS™ scanning technology. Image Courtesy of Materialise
Latest News
April 28, 2024
Renishaw and Materialise are broadening their multi-year partnership with solutions designed to increase efficiency and productivity for production-grade printing on metal AM Renishaw systems.
At the heart of the collaboration is improved integration between Materialise’s next-generation build processor software tailored to the RenAM 500 series of metal AM systems as well as with Magics, Materialise’s leading data and build preparation software. The companies also integrated TEMPUS, Renishaw’s recently released scanning algorithm for the Renishaw RenAM 500 series, which enables the laser to fire while the recoater moves, saving up to nine seconds per build layer without sacrificing part quality.
“Both the TEMPUS™ technology and next-generation build processors provide significant increases in productivity, but if you combine them in one solution instead of in isolation from each other, the benefit for the user is maximized,” explains Karel Brans, senior director of partnerships at Materialise. “With the release of Renishaw TEMPUS™ and Materialise's next-gen build processors, we recognized an opportunity to enhance our partnership and offer existing and new customers seamless integration between both technologies.”
Combining the technologies helps eliminate steps in workflows and avoid silos, enabling more scalable manufacturing processes that are efficient and error-free. Moreover, the combined solution enhances the handling of large data, which is increasingly common in the production of complex end-use parts, particularly those containing lattices and textures, Brans says. Specifically, build processors play a crucial role as they bypass the need to process tessellated data, ensuring smoother and more streamlined production workflows.
The new build processor will also make new Magics capabilities available as fully-integrated worksflows with the Renishaw AM platform. For example, the upcoming Magics release will include new functions for metal build preparation, including a new Simulation module powered by ANSYS, as well as integration with Metal eStage+, workflow automation and new lattice generation capabilities. These solutions help automate metal 3D printing to make it more cost efficient, but also lower the threshold for new user adoption.
The combined solution also delivers higher levels of control for users. Renishaw customers will be able to work directly on the underlying next-gen build processor software development kit (SDK), which enables them to craft custom build strategies for new materials or applications, all perfectly integrated with the Materialise and Renishaw ecosystem. “We have seen from in-house experience working with next-gen build processors that expert users who deeply understand the process and their specific application can achieve significant increases in productivity and quality on specific parts by optimizing build strategies,” Brans says.
Collaborations between technology providers are increasingly essential to fuel more widespread adoption of AM. Integrations help move the industry away from siloed systems, which is key to scaling AM to production-grade workflows as manual steps are more likely to introduce errors. Materialise’s build processor serves as a vital link in the workflow from Materialise Magics and the CO-AM software platform, which is a centerpiece for connecting all data within an AM factory and seamlessly integrating it with other business and manufacturing systems.
“The build processor eliminates unnecessary steps and streamlines processes,” Brans explains. “Moreover, it enables users to standardize their workflows across different types of 3D printers while leveraging the unique capabilities of each machine. This facilitates easier adoption of new machines at large AM factories, ensuring smoother operations and enhanced efficiency.”
For a look at Renishaw's TEMPUS™ technology, check out this video.
More Materialise Coverage
Subscribe to our FREE magazine,
FREE email newsletters or both!Latest News
About the Author

Beth Stackpole is a contributing editor to Digital Engineering. Send e-mail about this article to [email protected].
Follow DE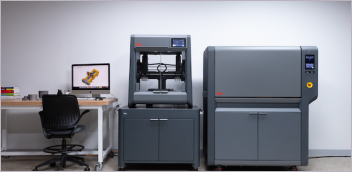
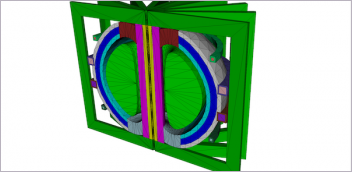
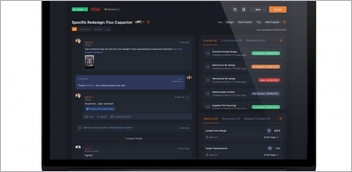
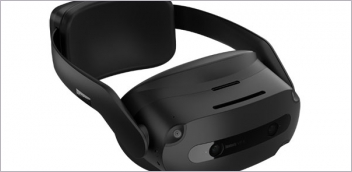