
Titanium implant encompassing part of a sternum and ribcage created through additive manufacturing. Courtesy of Anatomics.
Latest News
September 15, 2015
While important, 3D printing has yet to hit its full stride in some fields. The same cannot be said for use of additive manufacturing (AM) in the medical field. Doctors and researchers are continually dreaming up with new ways to improve the lives of patients by leveraging the power of AM.
Two months ago, a 54-year-old Spanish man went into surgery at Salamanca University Hospital for chest wall sarcoma. A cancerous tissue had grown in his chest cavity, encompassing part of his sternum and ribcage. To completely remove the cancerous growth, doctors would have no choice but to remove bone along with tissue.

Doctors realized what had to be done during the planning and discussed the best manner of creating bone implants to replace the complex skeletal structures they would be forced to remove.
“We thought, maybe we could create a new type of implant that we could fully customize to replicate the intricate structures of the sternum and ribs,” said Dr. José Aranda. “We wanted to provide a safer option for our patient, and improve their recovery post-surgery.”
Likely inspired by stories of other successful implants created using AM, the doctors took their idea to Anatomics, an Australian-based company known for its expertise in using data from CT scans to create surgical implants.
“While titanium implants have previously been used in chest surgery, designs have not considered the issues surrounding long-term fixation,” said Andrew Batty, CEO at Anatomics. “Flat and plate implants rely on screws for rigid fixation that may come loose over time. This can increase the risk of complications and the possibility of reoperation.”
Using the data provided by the surgical team, Anatomics created a 3D design consisting of “… a rigid sternal core and semi-flexible titanium rods to act as prosthetic ribs attached to the sternum.” The actual job of printing out the implant was given over to CSIRO and its new Lab 22.
Upon receiving the implant, doctors began surgery and found the titanium ribcage and sternum fit perfectly into place. The surgery was declared a complete success and the patient was discharged after 12 days in the hospital. A description of the procedure has been published in the European Journal of Cardio-Thoracic Surgery.
Below you’ll find a video about the implant.
Source: Anatomics
Subscribe to our FREE magazine,
FREE email newsletters or both!Latest News
About the Author
John NewmanJohn Newman is a Digital Engineering contributor who focuses on 3D printing. Contact him via [email protected] and read his posts on Rapid Ready Technology.
Follow DE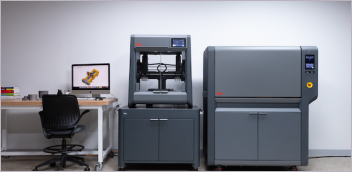
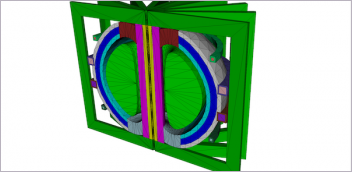
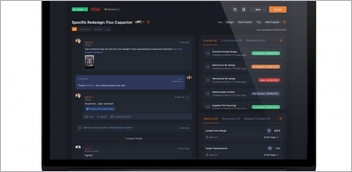
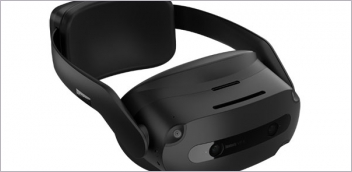