
The effect skin in the foreground (note the swirl design) is the result of 3D printing. Courtesy of Stratasys.
Latest News
June 24, 2016
I’m not really a car guy. As long as my vehicle is running, is generally clean, and isn’t covered in rust, I’m pretty happy. For those more attached to their rides, automotive customization offers an array of options which allows them to personalize their automobiles. Customization is also an extremely lucrative market that has generally been dominated by third-party companies.
Daihatsu is attempting to attract some of the market back to itself by testing the waters of automotive customization, thanks to additive manufacturing (AM) and with help from Stratasys. The automobile manufacturer is offering a limited selection of effect skins for the Copen, a two-door roadster that first went into production in 2002. The skins will be one of the first 3D-printed parts to even approach mass production for the automotive industry.

The effect skins are panels that replace portions of the front and rear bumpers and fenders of the Copen, giving each vehicle a different look. Daihatsu worked with Znug Design to develop the effect skins, and customers are further able to customize each skin themselves, leading to more of a one-of-a-kind appearance. Designers created 15 different effect skins, each available in 10 different colors.
Effect skins will be produced on Stratasys’ Fortus Production AM system in ASA thermoplastic, and the option would not be available without the flexibility offered by 3D printing.
“What would have taken two to three months to develop can now be produced in two weeks,” said Osamu Fujishita, Daihatsu Motor Co., Ltd. “We believe on-demand production [with 3D printing] offers definite benefits to supply chain efficiencies, and it allows easy access for customers.”
While certainly exciting for people who love their cars, the effect skin project is currently undergoing testing in select markets, and won’t go into full production until early 2017. Daihatsu isn’t the first automobile manufacturer to offer customization via 3D printing, and it certainly won’t be the last. While it may take a few more years for AM to make its way onto the factory floor for full-scale production, it has already found a place in the industry.
Below you’ll find a video about Daihatsu’s new customization options.
Source: Stratasys
Subscribe to our FREE magazine,
FREE email newsletters or both!Latest News
About the Author
John NewmanJohn Newman is a Digital Engineering contributor who focuses on 3D printing. Contact him via [email protected] and read his posts on Rapid Ready Technology.
Follow DE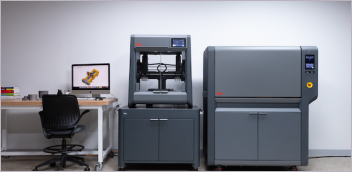
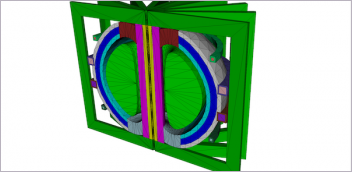
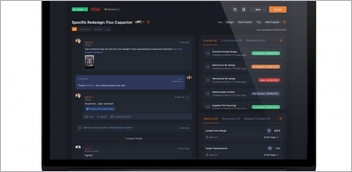
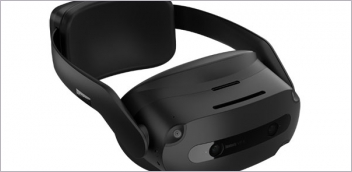