Latest News
May 14, 2012
By Lothar Kroll, Joerg Kaufmann and Norbert Schramm
Editor’s note: This article was originally published in German in Infoplaner magazine from ANSYS channel partner CADFEM.
When designing frames for premium bicycles, engineers must take into account a large number of characteristics, including strength, stiffness, weight, durability, ease of manufacture, type of bike and rider preference. Frames can be constructed from metals such as steel, aluminum or titanium, or they can be made of composite materials that are based on carbon fiber.
![]() |
An HTX Lector Team mountain bike from Ghost Bikes. (Image courtesy of Ghost Bikes GmbH) |
Traditionally, the use of conventional simulation in the bike industry has been limited to the metallic materials. However, scientists at the Institute for Lightweight Structures (IST) at Germany’s Chemnitz University of Technology used engineering simulation to successfully identify the stresses for a carbon-fiber reinforced mountain bike frame for Ghost Bikes GmbH—builders of premium bikes in all classes and categories. The research team used ANSYS Composite PrepPost software to analyze potential failure within the complex lightweight structure.
![]() |
A segmented model of the bicycle frame. |
Carbon-fiber reinforced polymer (CFRP) is an increasingly popular material for mountain bikes because of its lightweight characteristics and ease of manufacturability. In addition, fibers can be oriented to better withstand loads, and provide weight-efficient parts with high stiffness that will increase the overall stiffness of the frame—a desirable characteristic. To optimize the use of materials and to determine fiber orientation, complex calculations are necessary, and numerical simulation methods are required. Conventional composite simulation programs usually require additional work to define fiber orientations and define the plies.
ANSYS Composite PrepPost software, integrated within the ANSYS Workbench environment, takes advantage of outstanding features and solver technologies from ANSYS. This software substantially simplifies analysis of CFRP structures by using innovative modeling and analysis capabilities.
Assessment of Load Cases
To perform an effective numeric simulation, the engineer needs to determine the exact loads, boundary conditions and acceptable stress levels for a given component. The technical requirements and corresponding test procedures are defined by standards from the German Institute for Standards (DIN EN 14766 and DIN Plus for mountain bikes). However, these norms do not consider all possible loads the structure experiences, so the current research projects at IST were developed to expand the scope of these tests. The IST team defined three major load cases: brake, saddle and handlebar loads.
![]() |
Strain gauges used for testing. |
Engineers at IST created a model of the bicycle frame with Pro/ENGINEER Mechanism Design Extension (MDX). They used simulation to investigate transient loads, as well as seven quasi-static load cases. To optimally define the local material properties, they further sliced the frame into components using ANSYS DesignModeler software. The final verification of the simulation model was made using strain gauges and a test rig at Ghost Bikes.
Simulation in ANSYS Composite PrepPost
Researchers transferred the model they created to ANSYS Composite PrepPost using ANSYS Workbench. For defining specific composites in the bike’s frame, Composite PrepPost offers a variety of capabilities for both pre- and post-processing composites structures. The material definitions, including parameters required for a failure analysis, can be manually input or imported from a material library, such as the one available in ESAComp software (from Componeering Inc.) for analysis and design of composites. These material definitions can define fabrics, laminates or sublaminates (a combination of fabrics and laminates) with various properties, including thickness and fiber orientation.
![]() |
A laminate configuration predesigned using ESAComp, left, and the corresponding definition in ANSYS Composite PrepPost software, right. |
For the failure analysis of the bike frame, the IST team compared 16 laminate configurations to standard carbon fiber for high stiffness and resistance. The material assignment for the simulation model was applied on oriented sets. These groups of elements could overlap.
For each group, the team defined the global draping directions, as well as the definition of the zero-degree angular direction. Using Composite PrepPost made it possible to adapt the fiber direction for each element group using a smart combination of Cartesian, cylindrical or spherical coordinate systems.
![]() |
The definition of zero-degree fiber direction—with the help of a combination of Cartesian coordinate systems. |
The post-processing capabilities of Composite PrepPost are impressive: The large number of state-of-the-art failure criteria available, as well as the ability to perform layer-wise analysis of the results, allows the user to identify critical areas along with the load case for which failure might occur. Moreover, the use of the Cuntze and Puck criteria allowed the team to predict failure in the most critical areas.
Engineers investigated several variations of the design, using different configurations of plies. As a result of the simulations, the team designed an optimized frame that was able to meet the stiffness requirements—but would be cheaper to manufacture than the initial design.
![]() | ![]() |
An inverse reserve factor using Cuntze failure criteria; critical areas appear in red. | An inverse reserve factor of the optimized design. |
With ANSYS Composite PrepPost, the stiffness and resistance characteristics of fiber-reinforced bicycle components can be optimally adapted to meet design requirements and, furthermore, design efficiency is significantly improved. Compared to typical trial-and-error development methods used in the bicycle industry, the number of cost- and time-intensive physical prototypes was greatly reduced.
Dr. Lothar Kroll is full professor and Joerg Kaufmann and Norbert Schramm are research assistants for the Institute for Lightweight Structures, Chemnitz University of Technology, Chemnitz, Germany.
More Info
Chemnitz University of Technology’s Institute for Lightweight Structures
For more information on this topic, visit deskeng.com.
Subscribe to our FREE magazine,
FREE email newsletters or both!Latest News
About the Author

DE’s editors contribute news and new product announcements to Digital Engineering.
Press releases may be sent to them via [email protected].
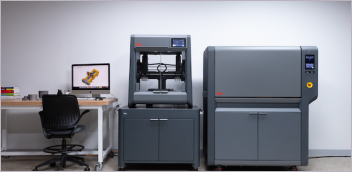
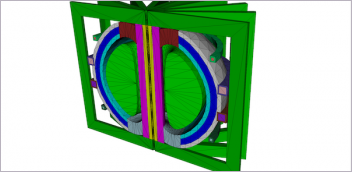
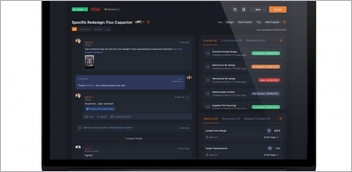
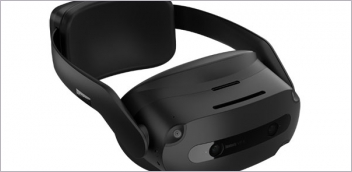