HP Puts 3D Printed Parts into Its Own Machines
HP rethinks manufacturing strategy to test the economics of additive manufacturing

The new 3D-printed part shown here, produced with HP Jet Fusion technology, replaces 7 disparate parts—an example of the use of AM for part consolidation. Image courtesy of HP.
Latest News
April 16, 2019
Would a 3D printer maker eat its own words? In other words, would a company championing additive manufacturing (AM) puts 3D-printed parts into circulation in its own products? That would certainly be one way to prove its confidence in the technology as a suitable means to produce end-use parts, not just prototypes.
HP decided to do just that.
“Our Jet Fusion 300/500 series 3D printers use more than 140 Multi Jet Fusion printed parts themselves, making it 'the printer that prints itself.' Because we’ve been able to minimalize tooling and assembly, we’ve created a 30% cost saving and cut development time in half,” says Scott Shiller, HP’s global head of customer and market development.
HP enters 3D printing
In 2015, HP announced it planned to become a player in the emerging 3D printing or AM business. Refashioning its tried-and-true 2D Inkjet technology into a powder-based 3D printing system, HP calls it Multi Jet Fusion. HP says one of the distinguishing features of its technology is voxel-level control.
“In 3D printing, a voxel represents a value on a regular grid in a three-dimensional space, like a pixel with volume. Each voxel contains volumetric information that will essentially bring a product to life with the desired properties,” explains HP in its product page.
Identifying the right parts to print
There are 21 3D-printed parts inside the HP Indigo 12000 Digital Press printers churning out colorful wedding albums and brochures. The switch from traditional production to AM led to “80% cost reduction and 91% assembly reduction,” says Shiller.
Inside the HP Latex Printing group, the engineers replaced an aluminum sensor-holding component with a generative design optimized part printed in Jet Fusion printers. “The weight of the part was reduced by 93%, the carbon footprint reduced by 95%, and cost was cut in half,” according to Shiller.
Finding the sweet spot for AM
With injection molding, the initial setup is a heavy investment, but once the mold is created and the repeatable process is in place, per-unit costs becomes far more economical. Unless the part requires special materials only printing technology can offer, large-volume jobs tend to favor traditional manufacturing methods, such as molding or machining. It's important to understand the specific volume for which 3D printing offers an advantage.
“The HP Jet Fusion 4200 printing solution provided a break even point of 50,000 units, as opposed to injection molding,” says Shiller. “We also offer the HP Jet Fusion 4210 system, which offers lower operating costs and increase volume production capabilities, raising the breakeven point for large-scale manufacturing to 110,000 parts versus injection molding.”
The Jet Fusion 300/500 series comprising 140 3D-printed parts are full color 3D printers themselves, priced beginning $50K. They target the small and midsize product development teams, according to the company's press announcement.
Design for 3D printing
To deploy AM as a manufacturing strategy, the conceptual design phase is crucial. During this period, designers can design parts that take advantage of AM, which requires a mindset change, as Shiller sees it.
“For years we’ve been limited to what traditional manufacturing methodologies were able to do for us, and now we must open our minds,” says Shiller. “It goes without saying that the widespread use of 3D printing creates a demand for new design skill sets and unlearning in many cases what constraints have previously been established. Apart from new skill sets, there will also be a shift in existing roles. For engineers, new elements of the design process will be introduced into their roles where they will need to learn the mechanics of 3D printing to become experts in the processes to support operational functions during production.”
Notes: Industrial scale 3D printing was the topic of the recent DE Hot Seat webcast. To listen, go here.
More Hewlett Packard Coverage
Subscribe to our FREE magazine,
FREE email newsletters or both!Latest News
About the Author

Kenneth Wong is Digital Engineering’s resident blogger and senior editor. Email him at [email protected] or share your thoughts on this article at digitaleng.news/facebook.
Follow DE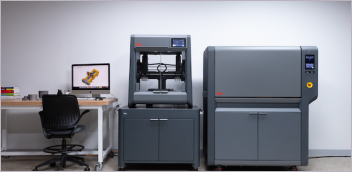
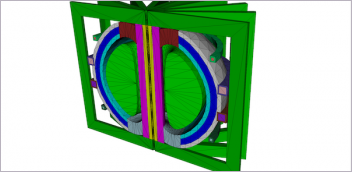
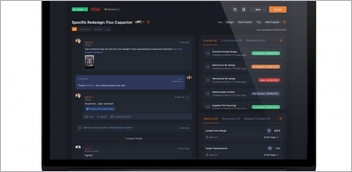
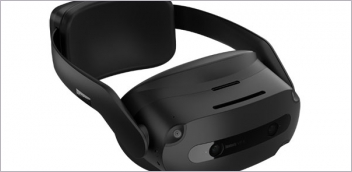