Latest News
September 1, 2012
By Lynn Manning
What’s the most important safety device in your car? Did you answer seat belt or airbag?You might be correct on a sunny day. But you can’t safely drive a single city block in a rainstorm or blizzard without your windshield wipers.
And they’re not only found on cars: planes, trains, boats, off-road vehicles and even space shuttles use windshield wipers. While the blades need periodic replacement, the wiper system itself is considered one of the most reliable of vehicle devices, with a design life average of 1.5 million wipes.
Designing Reliability
Reliability is a key tenet of Hyundai Motor Co. Founded in 1967 and headquartered in Seoul, Korea, the automaker keeps a sharp eye on every detail affecting motorist safety. The windshield wiper has been the focus of considerable attention at the company’s R&D center.
“We are looking to optimize both wiping performance and fatigue life of the windshield wipers on every vehicle Hyundai makes,” says Hyundai research engineer Sungjin Yoon. “To achieve that, we need to consider all the critical design factors, such as blade shape, material and the structure of the wiper arm and links. Computer-aided engineering (CAE) plays a central role in that process.”
Using a variety of CAE tools to evaluate the geometry, kinematics, loads and stresses on wiper mechanisms during the initial design stages helps Hyundai engineers meet current wiper performance guidelines. The tools also let them predict the effects of design modifications employing new materials, light-weighting, and/or innovative wiper configurations. Early identification of the most efficient design for each new vehicle concept both speeds up the product development process, and reduces prototyping and manufacturing costs downstream.
Sweeping through the Physics
At the core of the team’s CAE work is realistic simulation with Abaqus Unified finite element analysis (FEA) from Dassault Systèmes’ SIMULIA brand.
“The physics of windshield wipers are more complex than you might think,” says Yoon. “Previously, we’d been performing separate analyses for wiping and durability using two different FEA programs on two different computer models, but we wanted to develop a unified analysis model with which we could study both. We found that Abaqus has a full range of simulation capabilities that allow us to analyze every aspect of the characteristics we were interested in studying within a single software package.”
In addition to its essential back-and-forth behavior, a windshield wiper must, above all else, maintain uniform distribution of pressure between the windshield glass and the wiper blade so the driver’s view remains clear (this is known in some engineering circles as “the squeegee effect”). As the blade ages, it must continue to provide a certain level of cleaning ability. Plus, the entire wiper system needs to be strong enough to withstand a variety of loading conditions—from wind-driven rain to heavy snow—and durable enough to last for many years of operation.
Where the Rubber Meets the Glass
To begin their unified FEA inquiries into how wiper design affects both wiping and durability, the Hyundai team starts by looking at the rubber blade alone. To accurately predict wiper blade performance, it’s important to use a material model that fully captures the behavior of the rubber. The rubber material exhibits nonlinear elasticity, as well as a certain amount of time-dependency in its response. Capturing both these phenomena together was accomplished with a combination of hyperelasticity and viscoelasticity material options available in Abaqus.
Next, the engineers model the wiper arm system, a highly interdependent series of links and arms that combine to provide uniform pressure over the full length of the rubber blade. This is important for avoiding those annoying streaks on the windshield. To facilitate their FEA modeling, the group uses kinematic visualization software with a specific template for each vehicle wiper arm type.
Then the team is ready to run full Abaqus models to evaluate wiping. The first step is to properly load the wiper blade against the windshield to establish the correct initial contact pressures against the glass (see Figure 1). The axial connector element in Abaqus is used to express the behavior of the arm spring.
![]() |
Figure 1: Windshield wiper positioning analysis. |
“It’s important to establish what the preloading strain is,” says Yoon, “because it needs to be taken into account as the wiper moves, when the deformation shape of the blade section on the glass will affect the results over the total wiping area.”
A rotational moment is loaded at the base of the wiper arm to replicate the motor torque, at the point where the arm pivots. This causes the arm to slide across the glass with a wiping motion. The analysis can subsequently track the total strain on the blade at specific times and varying temperatures (the latter can particularly affect blade rubber). Final outputs are reported through an in-house post-program that shows the pressure distribution throughout a complete sweep of the windshield glass. (See Figure 2.) These results can then be compared against established design specifications to determine whether the blade is performing as expected.
![]() |
Figure 2: Wiper and glass model (left). Results of a wiper analysis, showing pressure distribution for both passenger (middle) and driver (right). |
“Clear” Results
The second part of the analysis, for durability (fatigue life), can be performed on the same FEA model that was set up for the wiping sequence.
“All we need to do is change the boundary and loading conditions in our Abaqus Unified FEA model,” says Yoon.
Just as was done with the wiping analysis, a rotational moment is entered as a loading condition. But this time, stationary “snow blocks” are mounted to halt the wiper blade before the lower and upper extremes of its sweep across the windshield glass model. As the analysis is run, the moving blade arm contacts the snow blocks, and the resulting internal forces on the linkage as the blade stops can be determined.
Stresses corresponding to these internal forces are used to predict fatigue life during moderate snow conditions or, in the case of heavy snow, plastic deformation or failure within the wiper assembly. These predictions are then validated under real-world conditions that include actual snow deposited on the windshield of a typical mass-produced car in Hyundai’s test facilities. (See Figure 3.)
![]() |
Figure 3: Indoor “snowstorm” at Hyundai R&D center (left) recreates the conditions that windshield wipers are designed to withstand. Snow block (in red at left) analysis duplicates these conditions to guide early design. |
Optimizing Wiping and Durability
With their wiping and durability results in hand, engineers can then optimize both factors by varying different design parameters and observing their effect on the overall performance of the wiper system.
“The superiority of the unified analysis model is that it enables us to consider a wide range of design factors affecting both wiping and durability,” says Yoon. “With an optimized blade arm and link combination, we can achieve a lighter-weight wiper system—while also increasing key link stiffness measures and reducing maximum stresses.” (See Figure 4.)
![]() |
Figure 4: Comparison of FEA results for wiper arm and link, before and after optimization. |
Hyundai’s R&D group is continuing to expand its use of templates to speed the windshield wiper design workflow. The Abaqus analyses are contributing to the buildup of a knowledge base with parameter studies that give the group better insight into which design variables have the greatest effect on component operation. All this points to their customers’ having a very clear view of the road ahead—in any weather.
Lynn Manning is vice president of Parker Group, a public relations firm based in Providence, RI, that represents Dassault Systèmes’ SIMULIA Corp.
More Info
Dassault Systèmes
Hyundai Motor Co.
Subscribe to our FREE magazine,
FREE email newsletters or both!Latest News
About the Author

DE’s editors contribute news and new product announcements to Digital Engineering.
Press releases may be sent to them via [email protected].
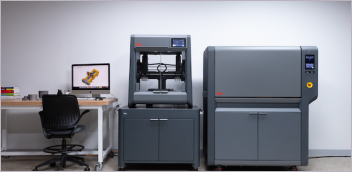
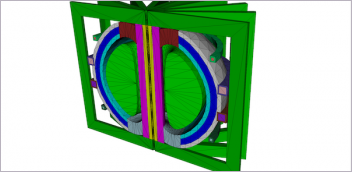
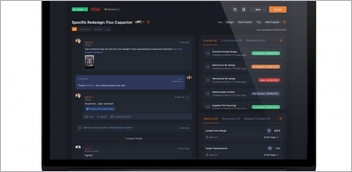
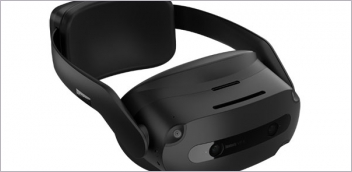