3D Systems Launches Figure 4 AM Solutions, Targets Enterprises with Different Degrees of AM Readiness

3D Systems introduces Figure 4 3D printing platform, aiming to evolve the technology from prototyping to production use (image courtesy of 3D Systems).
Latest News
November 9, 2017

In his 1984 patent titled “Apparatus for production of three-dimensional objects by stereolithography (SLA),” Chuck Hull, who cofounded 3D Systems, illustrated his concept in a series of figures. Back then, he might not have anticipated that, thirty three years later, one of the figures attached to the parent, Figure 4, would become the name for a series of 3D printing solutions.
This week, 3D Systems officially launched Figure 4, described as a scalable 3D printing platform.
“Not all the customers are at the right maturity level for AM adoption,” said Vjomesh Joshin (VJ), CEO and president of 3D Systems, in a meeting with the investors and industry press this week at the company’s headquarters in Denver, Colorado. “Their needs range from functional prototyping to low production to high volume production. So depending on the need, they’ll be able to pick the product configuration they want.”
The so-called platform comprises hardware, software, materials, and services. The initiative is aimed at shepherding the use of additive manufacturing (AM) from prototyping to mid- to high-volume production.
The Path to 3D Printing with Figure 4
The configurations of Figure 4 target different types of enterprises:
- Figure 4 Standalone, for companies that need affordable low volume production and fast, accurate prototyping;
- Figure 4 Modular, for enterprises that need a single high throughput 3D printing capacity.
- Figure 4 Production, for enterprises that want customized, automated high-volume 3D production as part of their manufacturing workflow.
Whereas Figure 4 Standalone is meant for businesses that need prototypes and mockups to test design ideas, Figure 4 Modular could be ideal for service bureaus with variable needs. According to Shultz, “The modular system can grow as you go, where you’re still not about volumes or customers. A prime example of that is 3D printing service bureaus.”
For customers who want to implement Figure 4 Production, 3D Systems plans to offer consulting and implementation services. “Some of these [consultants] will be our employees, our own application engineers,” said Shultz.
“In areas like healthcare-related [system, part, and process] validation and certifications, it can get complicated because the regulatory rules vary from region to region. That’s where we may bring in third-party partners with the domain and local knowledge,” said Greg Elfering, VP of Americas, production printers, 3D Systems.
From Prototype to Production
Though initially a rapid prototyping technology, 3D printing is gradually evolving into a full-scale production method in certain areas. With improvements in printing speed and metal-based print material quality, the technology is expected to gain wider adoption in aerospace, automotive, and other industries that had traditionally relied on machining and tooling.
For sculpting one-of-a-kind organic shapes, AM proves remarkably affordable compared to traditional manufacturing methods used for duplicating thousands of units of parts. Therefore, AM emerges as a viable option to produce patient-specific surgical guides, surgical planning models, and dental products.
Figure 4 solutions include dental-specific materials, such as NextDent.
In 2014, 3D systems acquired Medical Modeling Inc., whose services and products became part of the company’s healthcare industry offerings.
CAD’s Critical Role in Additive Manufacturing Adoption
VJ describes software as “the glue” to AM-centric manufacturing. In its ambition to push 3D printing from prototyping to production, the company is seeking stronger partnerships with CAD software vendors.
“My view is, engineers are using CAD software from one of the major vendors ... They won’t want to learn a new software for 3D printing; they’ll probably just like to push a button to convert the CAD model easily into a 3D-printable file. This gives them the confidence that 3D printing can produce what they’ve created [in CAD]. We can’t be part of the CAD design workflow, but we do want to be part of the workflow for inspecting and creating the part in the machine. So we’ll expose our API to CAD vendors so that level of ease of use if possible.”
Currently 3D Systems’ software offerings include 3DXpert, for creating and producing metal parts for additive manufacturing. With this software, you can “seamlessly work with both B-rep (solid or surfaces) and mesh triangulation formats (e.g. STL). [Therefore you can] ... make changes to the model at any stage of the process, using history based parametric CAD tools,” the company writes.
The Hybrid Additive-Subtractive Factory
3D printing’s ability to affordably produce complex shapes opens up additional opportunities, but, in VU’s view, it can’t entirely replace the traditional subtractive manufacturing methods.
“Not all factories will become exclusively additive,” cautioned VJ. “Most likely, they’ll have both additive and subtractive. We offer both in our portfolio.”
The company also offers on-demand manufacturing services, used by clients who want to bolster their own production capacity with outside sources to meet peak demands. Its on-demand services cover not just rapid prototyping but also low-volume production runs.
Read more about 3D Systems in Tony Lockwood’s Editor’s Pick of the Week here.
Subscribe to our FREE magazine,
FREE email newsletters or both!Latest News
About the Author

Kenneth Wong is Digital Engineering’s resident blogger and senior editor. Email him at [email protected] or share your thoughts on this article at digitaleng.news/facebook.
Follow DE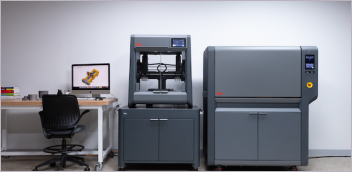
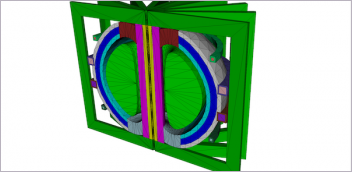
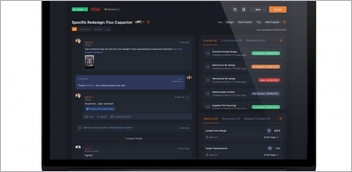
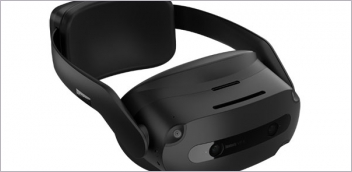