
This system combines additive and subtractive manufacturing to improve rapid prototyping. Courtesy of Hasso Plattner Institute.
Latest News
December 3, 2015
The strength of additive manufacturing (AM) lies in its flexibility. The technology is employed for a wide variety of end-use products, including everything from rocket engine parts to prosthetic limbs. That wasn’t always the case. Go back about six years and AM was mainly seen as a tool for rapid prototyping.
Rapid prototyping remains a valuable aspect of 3D printing, especially in engineering. Design iteration is faster than ever thanks to AM, allowing companies to fail early and more often at low cost. A collaboration between Cornell University and the Hasso Plattner Institute has resulted in a system that could reduce costs for rapid prototyping even further by refabricating existing prototypes.

The process, the subject of a scholarly paper titled “Patching Physical Objects,” involves a system that takes advantage of both additive and subtractive manufacturing processes. This allows designers to make changes to an existing prototype, rather than building a new one from scratch.
From the abstract:
Personal fabrication is currently a one-way process: Once an object has been fabricated with a 3D printer, it cannot be changed anymore; any change requires printing a new version from scratch. The problem is that this approach ignores the nature of design iteration, i.e. that in subsequent iterations large parts of an object stay the same and only small parts change. This makes fabricating from scratch feel unnecessary and wasteful.
The system accomplishes the task of “patching” objects in two stages. First, the designer creates a CAD file documenting the modifications to the original object and loads it into the system. The system then compares the differences between the original object and the updated object and calculates where and how much of the original needs to be removed.
The object is then inserted into the system, where it is milled to remove outdated portions of the design. Once that task is complete, the system then 3D prints new material onto the object resulting in an updated prototype. Researchers estimate users can reduce material waste by up to 93% by reusing prototypes rather than simply printing a new one for each iteration.
Below you’ll find a video demonstration of the process.
Source: Hasso Platner Institute
Subscribe to our FREE magazine,
FREE email newsletters or both!Latest News
About the Author
John NewmanJohn Newman is a Digital Engineering contributor who focuses on 3D printing. Contact him via [email protected] and read his posts on Rapid Ready Technology.
Follow DE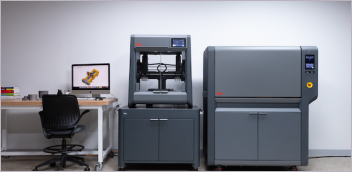
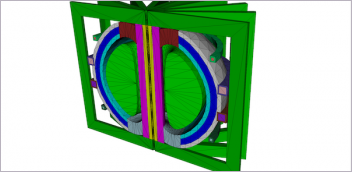
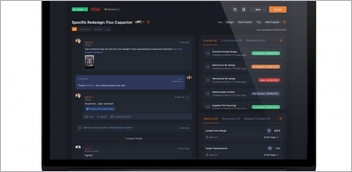
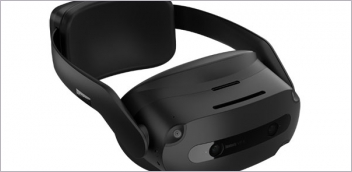