Latest News
May 14, 2012
By DE Editors
Innovaprep LLC, Drexel, MO, is a company with 16 employees that competes successfully against the giants of the defense industry by getting innovative products to market in less time. The company recently developed a portable air sampler designed to detect contaminants in environments ranging from the battlefield to food-processing plants. But the compact size of the product makes it difficult to produce a consistent flow regime in the outlet duct where flow measurements are taken.
That’s where simulation software comes in.
“We used SolidWorks Flow Simulation to diagnose flow inconsistencies in the original concept design, evaluate a series of proposed solutions, and ensure that our design met both uniformity and pressure-drop requirements,” recalls Zachary Packingham, an Innovaprep design engineer. “The result was that we saved prototyping and tooling cost, and got the product to market faster by getting the design right the first time. FISHER/UNITECH, our SolidWorks reseller, played a key role by helping us select the right toolset and helping us quickly overcome bumps we experienced along the way.”![]() |
Simulation of the sampler in a test chamber. |
Product Evolution
The idea for the new air sampler took shape when the U.S. Department of Defense issued a request for information for a battery-powered portable aerosol sampler. The project appeared to be a good fit with an Innovaprep-developed technology that quickly and efficiently removes particles from a membrane filter.
The company’s design uses a dry, 52mm electret filter as the collection media. Electret filters are produced from di-electric polymer fibers that develop an electrical charge when air flows past them. This substantially increases the collection efficiency of the filter, and allows for the use of lower-pressure drop filters, which, in turn, allows for higher sampling rates for extended periods using battery power.
![]() |
Simulation of flow in the inlet of the sampler. |
In the patented process for extracting the captured particles from the filter, a pre-pressurized cartridge containing an elution foam is attached to a quick-connect fitting on the cap of the filter cassette. The cartridge shoots wet foam through the interstitial spaces of the filter to efficiently extract captured particles.
“We were on an extremely tight budget and time schedule, and we were competing with mammoth defense companies in developing the air sampler,” Packingham says. “We didn’t have time or money to redesign and reorder components if they didn’t work right the first time, so we put extra care into the initial CAD design before any components were manufactured.
“In fact, when we started the company, one of the first things we purchased was SolidWorks CAD software, with the idea of modeling every aspect of our designs in software,” he continues. “We have regularly upgraded the software, and now use the current SolidWorks Professional 2012 because it includes the Toolbox standard component library and integrates with separately purchased Flow Simulation design analysis modules. Toolbox provides a wide range of standard parts, such as fasteners, that saves modeling time. Flow Simulation has proven to be valuable in identifying and diagnosing flow problems in the early stages of the design process. When we first started using the software, we ran into a few problems, and FISHER/UNITECH saved us a considerable amount of time by providing an immediate solution.”
![]() |
Simulation of the same inlet design at a different wind speed. |
Innovaprep engineers started the project by assembling a prototype using parts from other products that were available. They showed the prototype to the program office, and got the go-ahead to proceed. They began bench-testing technology they were thinking of using on the device, such as the filter holder and fan.
Packingham then developed several concept designs, and used the SolidWorks PhotoView rendering module to generate realistic renderings. He showed the designs to management, and a decision was made to complete one of the designs in full detail. He modeled every component in the design, down to fasteners and electrical connectors to make sure they would fit together. He used a SolidWorks assembly model to simulate the assembly process. He used models of hands and tools in conjunction with the model to make sure the device could be assembled, disassembled and serviced.
Just One Shot
Building the prototype required an extrusion die that cost about $10,000 and took six weeks to deliver. If the initial design had not worked, the company would not only have been out this cost, but would have missed the deadline for getting the project to the program office for review. So Packingham used SolidWorks Simulation to simulate the operation of the device.
The primary requirement for the inlet is the ability to capture biological particles in the size range of interest, such as anthrax or E. coli, while excluding uninteresting larger particles such as dirt and dust that might interfere with analysis. Packingham modeled the operation of the sampler in a virtual test chamber. He used the particle simulation tool in SolidWorks Simulation to release particles using different wind speeds and directions, and evaluated the ability of the sampler to capture particles of the proper size range.
![]() |
Rendering of the sampler in an open configuration. |
“We designed and modeled a number of different iterations of the inlet to make sure it primarily captured the particles that we were interested,” he says.
Outlet Duct Simulation
Packingham then modeled the outlet duct of the device, which has two important requirements:
1. The outlet duct is where flow measurements are performed. Ideally, the flow should be fully uniform across the duct, so that measurements will be the same regardless of where they are taken. In practice, though, it is difficult to keep flow uniform across a cross-section—and it is sufficient that there be at least one position in the outlet stream where the flow is proportional to the total flow, regardless of the flow rate. As long as this condition is met, it will be possible to make accurate measurements with a flow sensor at this position.
2. The second requirement is that the pressure drop in the outlet be kept low, to maintain high battery life.
Maintaining uniform flow was particularly difficult in the case of this sampler because of its compactness. There is a small fan in the center of the instrument and a battery below the fan. The air must make two 90° turns to get around the battery and the fan. Flow simulation showed that the air came out of the fan in a spiral pattern. When the air hit the first turn, the spiral broke down—and the vast majority of it hugged the far side of the wall. Then, when the air hit the second turn, the air moved to the other side of the wall.
Most importantly, when Packingham varied the air flow through the device, he saw that the flow patterns changed considerably: “There was nowhere that the sensor could have been placed where it could have provided accurate measurements over the full range of flow.”
The flow simulation showed that the root cause of the problem was the spiraling generated by the fan blades.
“The normal rule of thumb is to travel 10 times the diameter of the duct before the flow becomes uniform enough to take a measurement,” Packingham explains. “But the compactness of the sampler and the need to go around the battery made it impossible to travel much more than two times the diameter. I couldn’t move the battery because it would increase the size of the instrument beyond the requirements.”
![]() |
Rendering of the sampler in a closed configuration. |
There was no way to avoid the spiraling, so Packingham decided to position flow-straightening vanes between the fan and the first 90° turn. The vanes helped to make the flow more uniform across the cross-section of the sampler, but the first few iterations increased the pressure drop to the point that battery life would have been unsatisfactory.
Iterating to an Optimal Design
“I tried about 20 iterations with different shapes and sizes of flow straighteners,” Packingham recalls. “Viewing the simulation results, I came up with the idea of directing the flow up and down like a p-trap in a sink to increase the distance of travel. Space was tight, so I used the outside diameter of the fan as the inside diameter for the duct in which the flow travels up. Increasing the flow distance made it possible to reduce the invasiveness of the flow straightener, to the point that the pressure drop was reduced to acceptable levels. The new design had uniform flow at all flow rates, so measuring the flow rate was no longer a problem.”
Packingham notes that every part of the instrument was designed, analyzed and assembled in software before anything was made.
“As a result, the very first prototype of the instrument worked perfectly the first time—and we went from a napkin sketch to a fully developed and functional product in four months,” he notes. “This was no small feat, considering the level of technological innovation contained in this instrument and the limited resources we had as a small company.”
Unfortunately, cuts in the defense budget later caused the project to be shelved, but Packingham says that at press time, it is being launched for homeland security and food safety applications.
“A key to the success of this project was the use of CAD-integrated simulation to predict and diagnose the performance of a large number of concept designs prior to the prototype stage,” he concludes. “FISHER/UNITECH was instrumental by guiding us in the establishment of a strong in-house simulation capability, and helping us overcome obstacles that we encountered on the path to achieving our goal.”
More Info
Dassault Systèmes SolidWorks Corp
FISHER/UNITECH
For more information on this topic, visit deskeng.com.
Subscribe to our FREE magazine,
FREE email newsletters or both!Latest News
About the Author

DE’s editors contribute news and new product announcements to Digital Engineering.
Press releases may be sent to them via [email protected].
Related Topics
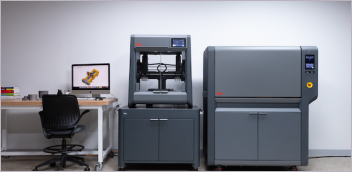
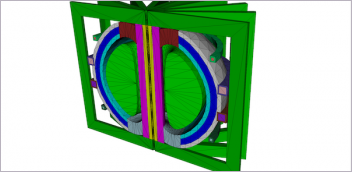
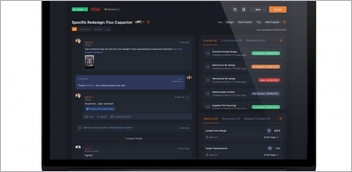
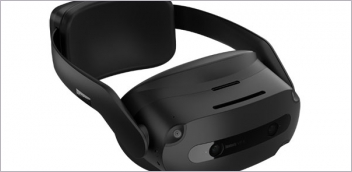