Latest News
March 1, 2012
By Kenneth Wong
From the way direct modeling has become the talk of the town, you get the feeling the technology is a newcomer, who arrived on the scene yesterday in a red sports car, with the top down. She got everyone hot and bothered with her push-pull action. She was simple, uncomplicated and easy to get along with. You could get to know her in just a day or two—sometimes in less than a few hours. You didn’t have to invest several years to know how to push her buttons. After a few sidelong glances, even some old-timers had to admit they were tempted to abandon their faithful parametric workhorses.
But here’s the kicker. Direct modeling is not new. She is the ex-girlfriend who’s lost a lot of weight and returned to conquer her old territories. Having shed the excess menus in previous interfaces, she’s now proudly flaunting her faster, leaner form. She has already captured the hearts of new users. Hobbyists, enthusiasts and 3D dabblers are waiting in line.
There is, however, a delicate dance she needs to perform: While winning fans with ease, she must figure out a way to get along with parametric modelers, who view her as a rival. If she wants to exert her influence over established communities, she can’t afford to alienate the history-based camp.
The Push-Pull Era
HP’s direct modeler, which sowed the seed for what would later become CoCreate (later acquired by PTC), was introduced in the 1990s. Kubotek’s KeyCreator, a direct-modeling pioneer, has been around since 2003. (Kubotek’s acquisition of the technology asset of CADKEY gave birth to the KeyCreator brand.) Explaining its approach, Kubotek writes, “Kubotek uses the intelligence inherent in geometry to power its Direct Editing. We call it Face Logic technology, a unique foundation for our advanced face selection capabilities. This means we are able to provide smart-editing tools that offer a very different approach to creating or changing a model. No history tree is needed to find features and manipulate the model geometry.”
Solid Edge with Synchronous Technology 4 is shown here with a model that
incorporates features built in a traditional history-based approach (Ordered)
and history-free approach (Synchronous).
For a decade or so, direct modelers like CoCreate and KeyCreator coexisted with history-based modelers, but they were rarely seen as serious rivals to the latter.
The watershed moment may have been SpaceClaim’s arrival on the scene in 2007. Many preceding direct-modeling programs relied heavily on dropdown menus and dialog boxes. By contrast, SpaceClaim’s push-pull approach made direct modeling much more direct. Want to move the location of a hole? Simply select the hole by its center axis, drag it along an axis, and release it at its new position.
Directly pushing and pulling on features and faces to edit or adjust their parameters is now the standard mode of operation in most direct-editing software packages. With some variations, this method is now employed by Autodesk Inventor Fusion, PTC Creo Direct, PTC Creo Elements/Direct Modeling, Solid Edge with Synchronous Technology (SE with ST), NX with Synchronous Technology (NX with ST) and others. Though known by different names (Copilot in PTC products, the Steering Wheel in Synchronous products, Dyna-handle in KeyCreator), the move-and-rotate handles in these programs are nearly identical. It invariably appears as three arrows pointing at the X, Y and Z directions, encircled in a rotation arc. Even some parametric packages that have been sitting on the sideline —for instance, Alibre Design and SolidWorks—employ methods that mimic the push-pull editing found in direct modelers.
Fundamentally Different Approaches
Direct modeling—the direct manipulation of geometry—is a departure from classic history-based, feature-based, parametric CAD modeling. In a parametric modeler, you rely on a series of steps to parametrically build your geometry. Want a cylinder with a hole? You sketch a circle in 2D, extrude the profile into a solid cylinder, sketch a circle on the top face of the cylinder, then use the circle to punch a hole through your solid. The information about the resulting shape is preserved in the history of steps you took to build the shape. Therefore, if you need to change something (say, adjust the diameter of the cylinder), you’ll need to retrace your steps to the point its parameter was first defined (in this case, the initial sketch), then make the edit there. This example deals with a fairly simple operation, but in complex operations, the geometry would have to regenerate, a process that could take time. That, more or less, is how parametric modeling works.
PTC’s Flexible Modeling Extension puts direct-modeling functions inside Creo
Parametric, a traditional history-based modeler (and the successor to Pro/ENGINEER).
In direct modeling, the emphasis shifts from modeling steps to geometry. In many direct modelers, you’ll probably still start off the same way you do in a parametric modeler. In fact, how you create your initial design in a direct modeler may even be identical to how you might do it in a parametric modeler. But when you need to make changes, direct modeling shows off its firepower. Because the software treats your geometry as, well, just geometry, you don’t need to rely on the feature history to edit your design. Want to adjust the diameter of your cylinder? You just select the base or top, then enter a new numeric value. If the software provides a dynamic dragging handle with real-time preview, you can simply push or pull on your geometry to widen its diameter. With this approach, you can execute a lot of complicated changes (like repositioning the location of a hole or rotating a surface) after the fact, with little or no regard for the modeling steps you’ve taken.
The strength of a history-based modeler is its ability to preserve the geometric relationships (such as coplanar and tangent faces) defined in the modeling steps you take. When you make an edit, most history-based modelers will regenerate the geometry in such a way so that the new geometry retains as much of the existing relationships as possible. When it can’t execute your edit without abandoning the geometric relationships, you get an error message, prompted by regeneration failure. On the other hand, in direct modelers, unselected geometry is not taken into consideration when you make an edit, so it’s up to you to do due diligence to make sure the edited geometry still retains the parallelisms, tangencies and alignments you wish to preserve.
Hybrid Aspirations
Two direct modelers with deep roots in history-based modeling—Autodesk Inventor Fusion and SE with ST—have been gradually bolstering features that let you move back and forth between direct modeling and parametric modeling. Inventor Fusion serves as a companion program to Autodesk Inventor, Autodesk’s classic parametric software for mechanical modeling. Over time, Autodesk plans to merge direct and history-based modeling into a single program, allowing you to work in both direct and history-based modes in a single program window.
At present, Inventor Fusion still remains a separate installation (it’s included at no charge when you buy Autodesk Inventor). But the company has put in significant efforts to convert direct edits made in Fusion into history-based features. In other words, if you execute a direct edit on your geometry in Fusion, once imported to Inventor classic, you could treat the feature as a parametric feature and continue to edit it using parametric editing methods. From the other direction, if you feel the need to make a direct edit while using Inventor classic, clicking on the Fusion button brings you right into Inventor Fusion.
With the option to work in Ordered (history-based) and Synchronous (history-free) modes in the same program window, SE with ST can justifiably claim to be the most advanced of the bunch in marrying the two modeling paradigms. The software’s robust feature-recognition technology and built-in algorithm (called Live Rules) let you identify and preserve parallel faces and matching curvatures, even if the use didn’t define them. Live Rules may also be temporarily suspended, so if you choose to break the inherent parallelism (such as extruded shapes on left and right that mirror each other), you can. These capabilities give the software a combination of flexibility and precision previously unseen in mechanical modeling programs.
A Break from History without Burning Bridges
In remaking its software titles into faster, lighter, nimbler apps, parametric powerhouse PTC introduced two direct-editing programs as part of its Creo 1.0 lineup. Creo Elements/Direct Modeling is derived from its previous product, CoCreate. Creo Direct is a brand-new app, developed from scratch. At present, the company promotes Creo Elements/Direct Modeling as a professional-class software, and Creo Direct for casual users within an engineering organization who would like work with 3D, but don’t need the full power (and complexity) of a full-blown CAD system. PTC’s long-term plan is to evolve Creo Direct to become the destination product for users of Creo Elements/Direct Modeling.
Though still a history-based modeler, SolidWorks offers you the choice to use
Instant3D’s push-pull editing, which mimics direct-modeling operations (demonstrated
here in SolidWorks Premium 2012). Instant3D is turned on by default.
In modeling strategy, Creo Direct and Creo Elements/Direct Modeling take an approach closer to SpaceClaim than SE with ST. When confronted with imported geometry, SE with ST makes certain assumptions about the inherent relationships in its geometry. For instance, if the imported geometry contains a series of holes that are aligned, the software will, in most cases, preserve the alignment. It also makes an effort to seek out nearby regions that may be affected by your edit (for example, blends that will be affected by the movement of a surface), even if you haven’t selected them for editing, then reconcile them with the edited geometry.
By contrast, PTC’s Creo Direct and Creo Elements/Direct Modeling treat geometry as a collection of solids and surfaces. If you’d like to preserve alignments and parallel structures in your geometry in these packages, you’ll have to explicitly tell the software to treat them as such. (One simple approach is to select and edit related features as a group.)
PTC also offers the Flexible Modeling Extension, a plug-in for Creo Parametric users. As a direct-modeler nested inside a parametric program, it takes a similar approach to Siemens PLM Software’s Synchronous Technology in detecting and honoring patterns and symmetries in imported models.
Is one approach better than the other? The answer depends on your own modeling preferences and the type of mechanical designs with which you routinely work. If you specialize in designs that include significant parametric constraints (geometric features that mirror each other on left and right, surfaces that must remain parallel or coincident, patterned features that must remain aligned, and so on), you may prefer a direct modeler that can deduce and preserve these relationships as you work. On the other hand, if you’d like to explore design alternatives with little or no concern for parametric constraints, you’d prefer the freedom of a direct modeler that treats geometry strictly as solids and surfaces.
New Markets for Direct Takeover
In the last several years, the do-it-yourself (DIY) movement picked up steam, fueled by trade shows like Maker Faire and subscriber-supported manufacturing facilities like TechShop. Driven to build one-of-a-kind artworks and prototypes, those in the DIY community are now turning to affordable 3D printing service bureaus to literally solidify their ideas. These hobbyists, inventors, craft-makers, self-taught designers and weekend engineers represent a new market for 3D software makers. Parametric CAD vendors like Autodesk, SolidWorks and Alibre Software are carefully watching the trend.
Creo Direct 1.0 from PTC, is a history-free direct modeler built from scratch,
according to PTC. The software is aimed at casual users who would like work
with 3D, but don’t need the full power and complexity of a full-blown CAD system.
The time and effort required to master a traditional parametric CAD modeler is more than what a DIY-er may be willing to spare. What these users need is a general-purpose direct modeler with a low learning curve, packaged in a novice-accessible interface like Google SketchUp. Recognizing this, Autodesk began pushing a new direct-modeling software titled 123D, based on Inventor Fusion, to the DIY market. Similarly, Solid Edge recently launched a subscription service (beginning as little as $19.99 a month for access to the software) through a partnership with Local Motors, an online community that practices crowd-sourced automotive design. PTC’s Creo Elements/Direct Modeling Express, a lighter version of Creo Elements/Direct Modeling, can also be a strong contender for this market. It’s available as a free download.
Direct is Parametric, Say Some What are your thoughts? To chime in, visit the DE fan page on Facebook. |
Another market, one that SpaceClaim is vigorously pursuing, is the analysis users. Though well versed in simulation disciplines, finite element analysis (FEA) and computational fluid dynamics (CFD) specialists may not necessarily be proficient CAD users. Yet, they must routinely engage with CAD models to inspect them and sometimes edit them—to remove rounded edges, blends, and holes on a solid block, for example.
For these users, a parametric CAD program’s feature history is often a stumbling block. It prevents them from making the type of edits they need to do with efficiency. (Most likely, they can make these changes in a parametric program, but they’d have to dissect the history tree to understand the model’s structure first—no picnic for someone with limited CAD experience). A direct modeler like PTC’s Creo Direct or SpaceClaim that presents a design as a history-free collection of surfaces and solids, on the other hand, makes the simulation specialist’s job a lot easier.
Historical Roots
Solid Works, one of the best-known names in mechanical CAD, remains a staunch parametric modeler. The software contains Instant3D, a function that lets you push and pull on surfaces and edges to adjust their heights, depths and diameters. It mimics the editing method found in direct modelers, but the software is, in fact, performing parametric edits. Therefore, it won’t allow you to execute operations that violate the feature history.
At present, Autodesk and PTC, both with history-based modelers still in their portfolios (Autodesk Inventor and Creo Parametric), continue to straddle both markets, preserving their parametric user base as they refine and promote their direct modelers. Siemens PLM Software is charging headlong into the hybrid mode with SE with ST and NX with ST. The dual-mode (Ordered and Synchronous) possible in latest releases of Solid Edge signifies that the company is fully committed to the notion of hybrid modeling.
In the long run, the distinction between direct modeling and parametric modeling will probably disappear. User demand is bound to result in the incorporation of more direct-modeling operations into existing parametric CAD packages, blurring the line between the two. Furthermore, increased computing horsepower in engineering workstations allows forward-thinking software developers to let their software infer and predict what a user wishes to do, which can lead to simpler, cleaner interfaces with fewer menus and dialog boxes. Extruding a 2D profile into a solid block, for instance, previously required a series of menu choices and input. In many contemporary 3D modelers, the operation has become as straightforward as clicking on a 2D profile and dragging it upward to add volume.
Many veterans would point to the birth of PTC’s parametric workhorse Pro/ENGINEER in the 1980s as a breakthrough in the history of CAD. But even the pioneer itself is now going through a transformation, signaling another technology breakthrough is overdue. Once history-based modeling was the best alternative. Today, it remains an important part of design and engineering, but it’s no longer the only alternative.
Kenneth Wong is Desktop Engineering’s resident blogger and senior editor. Contact him via [email protected], at deskeng.com/virtual_desktop or via Twitter @KennethwongSF.
MORE INFO
Subscribe to our FREE magazine,
FREE email newsletters or both!Latest News
About the Author

Kenneth Wong is Digital Engineering’s resident blogger and senior editor. Email him at [email protected] or share your thoughts on this article at digitaleng.news/facebook.
Follow DE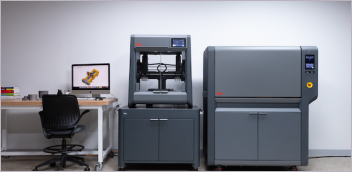
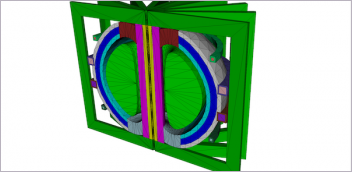
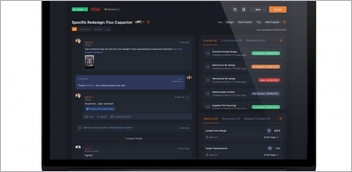
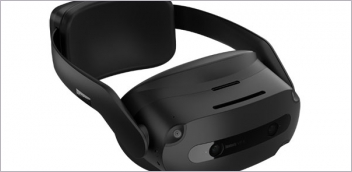