
ACS used this FDM fixture as a guide to drill holes in a helicopter.
Latest News
August 1, 2014
Advanced Composite Structures (ACS) repairs helicopter rotor blades and other composite structures for fixed- and rotary-wing aircraft. The company also produces low-volume production composite parts for the aerospace industry.
Both offerings require tooling. On the repair side, the company normally uses a mold with a contoured surface to guide the repair. It creates most production components by applying composite laminate strips onto layup tools. Many jobs also require fixtures to locate secondary operations such as drilling.
Old Methods
In the past, ACS typically produced layup tools, drill fixtures and consumable core patterns on computer numerically controlled (CNC) machines. Another option was producing a model using a CNC machine or power tools and using it to mold a composite layup mandrel.
It typically cost around $2,000 to hire a machine shop to produce a metal composite mold. Producing a model and molding a composite layup tool cost about the same. In both cases, lead times were eight to 10 weeks.
Initial tooling design sometimes presented problems, however. In these cases, ACS incurred substantial additional expenses — and the project was delayed while the tooling was repaired or rebuilt from scratch.
New Efficiencies
More recently, ACS has switched to producing nearly all of its tools using additive manufacturing (AM) on Stratasys’ Fortus Fused Deposition Modeling (FDM) machine. FDM technology is an AM process that builds plastic parts layer by layer, using data from CAD files. A typical FDM layup tool takes only about $400 and 24 hours to produce. The low cost and short lead time mean ACS can easily remake tools that are found to have problems on the manufacturing floor.
For example, ACS recently produced a camera fairing used to install a forward-looking infrared camera on a military aircraft. The Fortus machine built the layup tool directly from a CAD drawing. In another example, the geometry of a vertical fin assembly for a helicopter is so simple that a layup mandrel was not needed. However, the Fortus machine produced a drill fixture to accurately locate a series of holes.
ACS also used FDM-built tooling to fabricate a capsule component for a remotely piloted vehicle. The company built a consumable core, core co-bond tool, cover layup tool, cover trim tool and cover drill with the FDM material ABS-M30 thermoplastic.
The traditional approach to producing hollow composite parts is to use CNC machines to make patterns from polyurethane boards that are then used to mold clamshell tools. The FDM method offered substantial time and cost savings.
“Tools produced with FDM cost only about 20% as much as CNC-produced tooling,” says Bruce Anning, owner of ACS. “FDM tooling can be produced in a single day compared to several weeks for CNC tooling. For the repairs and short-volume production work that we specialize in, tooling often constitutes a major portion of the overall cost. Moving from traditional methods to producing composite tooling with FDM has helped us substantially improve our competitive position.”
More Info
Subscribe to our FREE magazine,
FREE email newsletters or both!Latest News
About the Author

DE’s editors contribute news and new product announcements to Digital Engineering.
Press releases may be sent to them via [email protected].
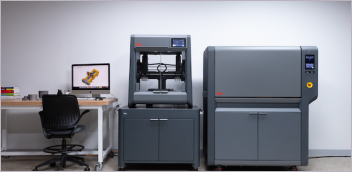
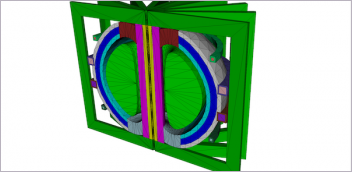
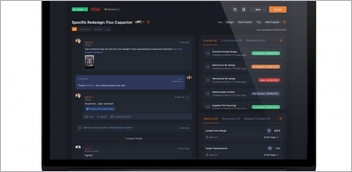
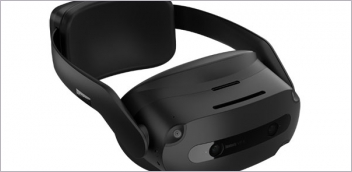