
Using a color-coded display, PTC Creo View makes it clear which items are on schedule, beyond schedule and released. Image courtesy of PTC.
Latest News
November 1, 2016

A major battle in engineering change management has already been fought and won. The struggle was between the style that favored data control and the approach that promoted collaborative product development. The former change management strategy, accomplished with a mix of file locking and access limits, is now supplanted by model-based design, only achievable by multidisciplinary collaboration involving a wider circle of stakeholders. The new struggle is to find efficient ways to offer transparency, facilitate collaboration (both asynchronous and real-time) and comply with myriad regulations (both regional and international).
Because smart products are becoming the norm, change management tools, such as PLM (product lifecycle management) programs, may need to keep up. Many vendors are incorporating augmented reality (AR), compliance check mechanisms and mobile applications to make change management easier.
A Low Threshold for Clunky UX
Now considered one of the greatest sins of user experience (UX) design, complexity was once a standard feature of enterprise software. Some vendors justified it as a necessity in tools that must juggle complex data transactions. Accepting it as unavoidable, and many users put up with it. But the mobile app culture changed that.
“The basic tenet in mobile apps is, it must require no training,” says Steve Chalgren, executive VP of Product Management and chief strategy officer at Arena Solutions. “But enterprise software didn’t have that rule governing it. So vendors added complexity without worrying so much about training. In fact, training was a source of revenue for many.”
The unspoken business rule today is if you’re not on mobile, you’re at risk of becoming irrelevant. And going mobile means adopting the golden rule of apps commerce: simplicity. The same applies to change management tools in PLM.
“The big change coming is not so much in the process but in UX,” says Chalgren. “We need to make it easy for people to understand what’s been changed [in the product design] so they can digest and approve it, in an app that needs no training.”
Most PLM vendors today offer mobile apps that perform a subset of the operations possible with desktop clients. Siemens PLM Software’s Teamcenter Mobility and PTC’s Windchill Mobile fall into this category. The vendors who don’t yet offer mobile apps generally facilitate mobile devices by supporting mobile-friend browsers. Dassault Systèmes currently doesn’t offer a mobile apps for its 3DEXPERIENCE platform and ENOVIA products, but they can be accessed and run from mobile web browsers. Beginning in the mid-2000s, Arena Solutions has supported mobile access to Arena BOMControl through mobile browsers.
PLM vendors with integrated CAD packages also tend to offer mobile CAD file viewers to allow those outside engineering to view, discuss, annotate and comment on 3D files with pending revisions and changes. Siemens PLM Software’s Solid Edge Mobile Viewer and JT2Go, PTC’s Creo View Mobile, and Dassault Systèmes’ eDrawings Mobile are examples of such apps.
Design Review in AR
With the advent of affordable augmented reality (AR) and virtual reality (VR) hardware, engineering teams now have another way to preview and study proposed design changes. “Design review is part of the change process,” says Francois Lamy, VP of PLM Solutions and Strategy at PTC. “Today, design review preparation is very time-consuming. PLM can facilitate the preparation tasks by collecting all the relevant information, including 3D representation and then leveraging AR to share the information and collect feedback to be integrated in the change process. This digital process will also facilitate collaboration.”
Through its AR-focused Vuforia division, PTC offers VuMark, part of Vuforia 6. “VuMark is a customizable visual code that can be affixed to any product or machine—either manually using a decal, or automatically printed during the manufacturing process,” PTC writes. “It is intended to visually indicate to a user that an AR experience is available, such as step-by-step instructions for assembly, use, cleaning, repair, inspection, etc.”
Lamy adds: “You can take the VuMark [a printed computer-generated icon that the AR app can interpret as a 3D model], view it from an iPhone or iPad to look at the changes and validate it. From an intellectual property (IP) perspective, it’s pretty interesting. You’re not sending out a CAD file; you’re sending a VuMark and sharing the AR experience with the participants in the design review process.”
Sending a CAD file or even a lightweight 3D model carries the risk of someone reverse engineering the product from the digital data. On the other hand, the VuMark, which operates like a QR code, doesn’t contain any 3D geometry that can be extracted. Therefore, it prevents the possibility of IP theft.
“VR can enable the simulation of the final experience of the product for various stakeholders—the user/operator, the maintenance people, and the manufacturing/assembly workers, for instance,” says Naim Dalal, senior ENOVIA UX manager at Dassault Systèmes.
Dassault Systèmes’ 3DEXPERIENCE platform offers technologies to display 3D data in immersive CAVE environments, or in specialized hardware like zSpace, a Dassault Systèmes partner. eDrawings Mobile from the company’s SOLIDWORKS division includes AR viewing tools.
AR-powered design review could also help tackle change impact from a knowledge standpoint. “If there are manufacturing deviations, for instance, those in the field may have to use a special technique to install a part,” says Bill Lewis, Siemens PLM Software’s director of Marketing. “That knowledge can be identified and captured in AR.”

Siemens PLM Software offers JT2Go, an in-house developed app to view 3D models in the widely accepted JT format on multiple hardware platforms, including the Microsoft HoloLens. The company allows third parties to harness its APIs (application programming interfaces). Light Guide Systems from OPS Solutions, a gesture-operated app recently demonstrated at Siemens PLM Software’s analyst event, is one of the resulting products. The AR-powered design review app offer an easy way to capture as-built conditions, which could be used to kick off the Corrective Action sequence.
AR-incorporated mobile apps could also be much more inclusive than shared CAD models. Whereas CAD software is largely confined to engineering and design, product data delivered in lightweight formats to mobile devices has a wider, more accessible audience. AR’s ability to merge pixel-constructed product models with real-world environments captured in the mobile device’s camera gives those outside engineering an easier way to understand the impact of design changes.
Cost and Compliance
One primary reason to closely monitor changes is to prevent potential cost overruns. “Early stage cost estimates tend to be pretty accurate, because they’re usually based on previous programs,” points out Lewis. “Then, because of engineering and design changes, the project may need more materials, or less; it may need a different manufacturing process. But engineers aren’t able to reflect on these consequences while they’re making the changes.”
Siemens PLM Software’s Teamcenter offers a Product Cost Management module. According to the product home page, the module can “calculate complex assemblies and versions accurately and quickly; reproduce the entire price structure of your products and variants based on the bills of materials (BOMs) and bills of process (BOPs); determine and itemize direct costs and overheads, manufacturing steps and processes and materials and process parameters.”
Furthermore, it includes “an extensive and cost-relevant database ... to simulate different scenarios, including production sites, machines, and pre-configured reference processes for numerous manufacturing technologies and cost rates.”
You can rough out the manufacturing process with the module, says Lewis, “using the time and cost it takes on a particular machine; you add the labor rate based on a region, whether it’s to be made in China or Germany, for example; you add material cost, energy cost and so on. So when you make a change, you can enter the change into the cost model, and it will give you a new cost.”

The increase in environmental regulation adds a new dimension to change management. “Every country is adding new environmental regulations—more and more,” says Lamy. “And every company is dealing with global product development. So project managers need to have good visibility into the compliance and sustainability content of their products.”
PTC addresses this with its Materials Compliance Solution, part of the company’s Windchill software. The product tackles, among other things, the regulations governing conflict minerals. PTC writes that it lets you “[perform] part, product, and supplier level analysis to ensure compliance with numerous evolving regulations and customer requirements; ... collect supplier data using automated data requests, industry standards, custom templates; protect revenue streams by making compliance risk analysis part of standard development processes; [and] demonstrate product and supply chain compliance ... with detailed, data-rich audit trails and reporting capabilities.”
“Compliance goes further than the CAD model; it affects the supply chain,” Lamy says. “If I’m going to design a product, I need to know which of the suppliers I can use to be compliant. I need to shop for suppliers based on my regulatory needs.”
Dassault’s Dalal notes that ENOVIA users can conduct a cross-functional change assessment process directly from the change order. “This capability provides the global team with a visibility on all related data that might be impacted by this change, such as: Where the [changed item] is currently being used/consumed, which specifications are related to it, the child parts (as noted in the engineering bill of materials, or EBOM), and so on,” he says. “ENOVIA also provides other impacted organizations within the company with a way to submit an impact analysis report that can include financial risks, impact on schedule/ quality, etc.”
Pricing and Progress
Aside from the technology, evolving PLM pricing practices may also widen the circle of change management. The shift from perpetual licensing and on-premise systems to subscription-based, cloud-hosted SaaS (Software-as-a-Service) style PLM allows a greater pool of users to participate in the discussions about change impact. Some established vendors in the PLM space, like Autodesk and PTC, offer modular PLM products on subscription. Aras offers its Innovator PLM solution for free, and then charges for pay-as-you-go training and consulting or an annual subscription that includes upgrades. Arena Solutions entered the market with a cloud-based multi-tenant BOM management product, BOM.com.
Change management tools in PLM have significantly improved, but many critical processes, such as impact analysis and cost control, largely remain manual; they rely on the expertise, diligence and timely input of the human reviewers to kickoff and complete the workflow. The next step in change management may be the development of rule-based, algorithm-driven tools, capable of not only spotting but also predicting cost overruns and manufacturing problems invisible to the naked eye.
“Ten years ago, impact analysis was mostly based on the parts used in an assembly. Today, it’s much broader,” Siemens PLM Software’s Lewis observes. “If you change a part, the ecosystem it lives in, has to be re-evaluated. The part is used in this assembly, but is manufactured in that plant, using this process, with this material, selling into these regions, governed by these regulations. All this knowledge is built into PLM, so the system is getting smarter. It has gotten the point where it can start suggesting things you should look at as alternatives.”
More Info
Subscribe to our FREE magazine,
FREE email newsletters or both!Latest News
About the Author

Kenneth Wong is Digital Engineering’s resident blogger and senior editor. Email him at [email protected] or share your thoughts on this article at digitaleng.news/facebook.
Follow DE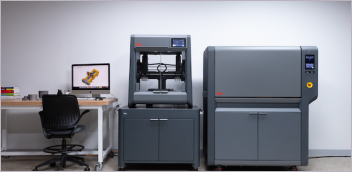
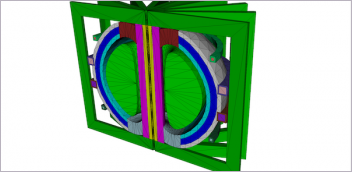
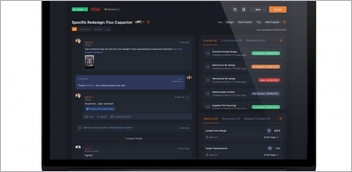
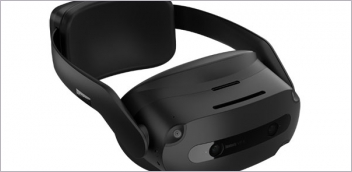