3D Printing Prep Gets into Shape

With Materialise Magics, users can convert 3D models to STL format, repair errors and prepare the build platform as part of the broader Magics 3D Print Suite. Image courtesy of Materialise
Latest News
May 1, 2017
Not many of us sweat about hitting the print button to output a document, but for those assembling presentations or other complex materials, there are copious formatting and file tweaks that need attention to ensure the final product is up to snuff.
It’s a similar situation in the world of additive manufacturing (AM). Despite the ease-of-use promises from a recent spate of office-style 3D printers, design teams that have spent years muscling through trial and error AM practices know there’s a ton of upfront model preparation and hands-on pre- and post-processing work required to ensure a successful build.
“It often comes across that 3D printing is as simple as pressing a button, but that’s not even remotely the case—there’s a great deal of work required to get a model in the shape it needs to be,” says Terry Wohlers, president of Wohlers Associates, an independent consulting firm specializing in AM and 3D printing. “There’s a perception that 3D printing is easy among people who’ve never done it, but people who are close to the machines and operate them have an appreciation for what it takes.”

The challenges surrounding 3D model prep vary depending on the type of 3D printing method—fused deposition modeling (FDM) with thermoplastics materials, for example, or direct metal laser sintering (DMLS), which uses powdered metals. With FDM and some other 3D printing methods, 3D models can run into trouble with edges that are not fully watertight (meaning adjacent surfaces around the perimeter aren’t meshed properly so the volume isn’t fully closed). DMLS and other metal-based AM methods can introduce their own set of design challenges to ensure there are no structures in place that trap loose powder materials upon printing. Proper orientation of the 3D model on the build envelope, nesting models properly to optimize a print build, and issues related to designing around support structures or powder drains are other factors to consider when prepping 3D models for 3D printing.
Most of these issues are typically addressed in the post-design process, often using additional editing software and file healing tools and involving multiple, disconnected steps, notes Jose Coronado, product management manager, CAD, at PTC. In a typical scenario, for example, a user would create a solid model in their CAD system and perform a conversion to create a triangulated model while potentially introducing lattice structures to reduce weight. From there, there is additional software required to slice the final model and create an STL file, the standard format most 3D printers understand.

“In this scenario, there are three different systems and the original part is no longer a solid model,” Coronado explains, adding that if you bring in topology optimization or finite element analysis (FEA) to validate and optimize the design, you might end up with five disparate programs. “For users with CAD and PLM systems, going through four or five systems to finally print a part makes it difficult to adhere to corporate processes,” Coronado says. Even worse, changing from solid to mesh can sacrifice precision or lose PMI (product and manufacturing information) that is needed downstream, he adds.
Vendors Heed the Call
As 3D printing gains traction as a method for prototyping and limited run production, CAD vendors like PTC and other specialty tool providers are adding capabilities that make it easier to prepare 3D models for 3D printing. PTC, for example, offers the AM extension for Creo, which executes critical steps in the CAD platform while also adhering to solid geometry standards (boundary representation or BREP geometry). The module has a feature called “tray assembly” that serves as a repository for AM-related data like positions, colors and materials to promote reuse and maintain file consistency along with lattice capabilities for creating lightweight designs that aren’t part of the initial solid without any compromise to stress or displacement. Finally, there are connectivity functions that ensure a bidirectional exchange of data between the CAD package and the 3D printer in real time to minimize the pain of file conversions, Coronado says.
Autodesk, as part of a major investment in 3D printing and AM technology, is easing the 3D model preparation burden through its Netfabb 2017 suite, an industrial-grade portfolio that spans model preparation, manufacturing simulation and design optimization used to create internal lattice structures for lightweighting parts. Netfabb enables engineers to import, analyze and repair models from a variety of CAD formats and identify areas that require supports. Netfabb can also be used to semi-automatically generate support structures and modify models so they are optimized for production, including the ability to adjust wall thicknesses and smooth rough areas—common pain points for 3D printing model prep, according to Duann Scott, Autodesk’s additive manufacturing strategist.

Another key capability of Netfabb is the ability to build repair scripts. “This is helpful for advanced engineers who want to help inexperienced engineers via access to a script,” Scott says. “There’s a black art in 3D manufacturing and this helps make that knowledge available to others.”
For its part, SOLIDWORKS 2017 also ushers in capabilities for facilitating 3D printing and 3D model prep. The Print3D option, which enables engineers to evaluate the build orientation of a part and export a SOLIDWORKS file to STL or the newer, high-fidelity and extensible 3D manufacturing format (3MF), has been enhanced with additional capabilities. Specifically, the tool has new analysis capabilities for determining support structure material as well as a thickness/gap analysis check, which flags small features or gaps that could possibility fail, particularly when creating a scaled down version of a part, says Mark Rushton, product portfolio management at Dassault Systèmes.
In addition to melding specific 3D print functionality into CAD programs, vendors are also focused on building bridges between CAD and 3D printing environments so that engineers can move seamlessly between the two. SpaceClaim’s STL Prep for 3D printing modules lets users work directly with STL files to shell and scale models or to split models to add features as needed as well as clean up common bad geometry issues related to wall thickness, watertight models and self-intersecting triangles, officials report. The module does so by leveraging all of the solid creation and direct editing tools familiar to SpaceClaim users. “Ideally, you want to go back and forth between solid models and STL files, but there’s not a one-to-one relationship,” says John Graham, product marketing manager at SpaceClaim, now owned by ANSYS. “This is the next best thing.”
Some industry players are addressing the CAD-to-3D printing integration challenge through partnerships like the one between Siemens PLM Software and Materialise, which markets Magics, long considered a standard for 3D printing model preparation. Earlier this year, the two companies showcased a technology demonstration to integrate some of Magics’ capabilities, particularly in the areas of lattice structure and support creation and nesting of models in the build platform, into Siemens NX CAD program to create a seamless experience for users, according to Bryan Crutchfield, Materialise’s vice president and general manager for North America.
3D printer manufacturers are also turning to the CAD world to ease 3D model preparation. Although Stratasys has offered the Insight software for years to prepare STL files for output on its Fortus FDM printers along with Catalyst for its uPrint and Dimension offerings, the company saw an opportunity to make a universal tool that worked across printer families. In addition, it wanted to make this part of the process more accessible to engineers and laymen who didn’t necessarily have the know-how or the inclination to learn Insight or who didn’t require its more advanced feature set, optimized for customized tooling use cases, says Allen Kreeme, head of application engineering for Stratasys.
Leveraging its GradCAD acquisition, the new GrabCAD Print lets users prepare, schedule and monitor 3D printing jobs across the Stratasys printer line with a simpler drag-and-drop interface and working with most native CAD formats. GradCAD Print, built on the open, cloud-based GrabCAD platform, is designed to streamline the design-to-3D print workflow by eliminating or minimizing the need to export files to the STL format, Kreeme explains. “Our goal with GrabCAD Print is to get to hit the most number of installed, office-friendly machines because that’s where people need the most help cleaning files,” he explains.
3D Systems is also looking to streamline and simplify the experience for users of its plastic and metal-based 3D printers. 3DXpert, the system for the metals-based offerings, is an integrated platform that covers the entire metal additive manufacturing process, eliminating the need to have multiple solutions to import part data, optimize lattice creations, calculate the scan path and arrange the build platform, according to Maoz Barkai, product manager for the software. The software also eliminates the need for working with STL or other mesh models, enabling users to prepare a part for printing using history-based parametric features. “When creating supports using CAD geometry, there’s no reason not to build it like you would in any other CAD system,” he explains. 3D Sprint, 3D Systems’ software for its plastic printers, also provides an array of analysis and repair tools and is focused on ease of use with the aim for push-button 3D printing, notes Scott Green, director of product management software for 3D Systems.

Although great progress is being made on the tool front, it’s actually the in-the-trenches experience and sharing of tribal knowledge that will advance 3D printing and make model preparation challenges a thing of the past. Wohlers suggests that companies start documenting design guidelines and 3D model preparation best practices in addition to leveraging the new genre of tools that facilitate and optimize important workflows. “Individuals have years of trial-and-error experience in their heads and increasingly they need to document this information so it can be passed on to others,” Wohlers explains. “The tools still have room for development and so does the talent—it’s just a matter of time.”
For More Info
Subscribe to our FREE magazine,
FREE email newsletters or both!Latest News
About the Author

Beth Stackpole is a contributing editor to Digital Engineering. Send e-mail about this article to [email protected].
Follow DE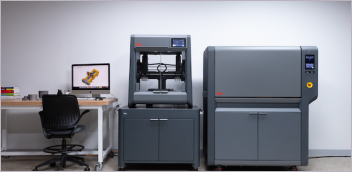
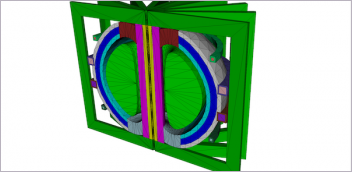
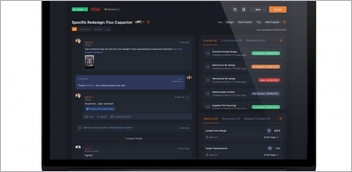
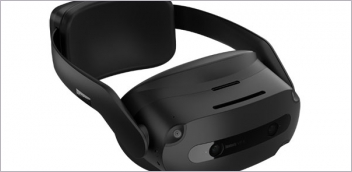